BRACKET & ACCESSORIES BONDING
APPLICATION OVERVIEW
Brackets, hinges and other accessories often need to be added to panels, doors and enclosures. These accessories are typically used in an assembly step after manufacturing. Plexus adhesives are used where metal and plastic brackets are required on RTM (composite) or ABS (thermoplastics) substrates. In these applications, Plexus adhesives offer a rapid “snap-curing”, with the ability to adhere to multiple or dissimilar materials.
Due to the loads after assembly, brackets are often points of high stress and large levels of fatigue. Plexus adhesives offer best in class fatigue resistance and the ability to evenly distribute the high stress points, which leads to long term durability.
Brackets are typically made of plastics, coated metal, aluminum, galvanized steel, or stainless steel. Plexus has adhesives that are primer-less to all those materials with an ability to cross bond to other materials such as:
COMPOSITE
Plexus adhesives have long been the leading choice for gluing composite materials. Plexus adhesives, bond or glue, to most composites with little to no preparation and offer primer-less adhesion to aluminum, stainless steel and zinc coated brackets. Plexus adhesives are designed with the optimal combination of strength and elongation to absorb different levels of thermal expansion, as well as long term fatigue to maintain part integrity.THERMOPLASTICS
Bonding bracket and accessories thermoplastics such as ABS, PS, Nylon, etc. requires adhesives that can bond both materials with little or no preparation. Plexus adhesives provide robust adhesion to most thermoplastics with no preparation steps.RAW METALS
Metal bonding adhesives can often be dispensed significantly faster than welding or riveting, leading to significant production and cosmetic gains. Plexus adhesives distribute stress over a greater surface area as compared to stitch welds, spot welds or rivets. Many manufacturers look to Plexus as their metal glue of choice. For more information on Plexus adhesives for metal bonding, please visit our Metal to Metal Bonding Page.
COATED METALS
There are numerous advantages of Plexus adhesives when bonding brackets treated with protective coatings. One of the greatest advantages is that Plexus is non-conductive.
Unlike mechanical fasteners, there is no need to create holes in the metal fastener and breach the integrity of the coating in order to use Plexus. As a result, Plexus adhesives provide an additional layer of corrosion control and eliminate the risk of Galvanic Corrosion. Another benefit is that Plexus adhesives distribute the stress load across the part, which puts less stress on the coating itself, this leads to longer product life and improved durability.
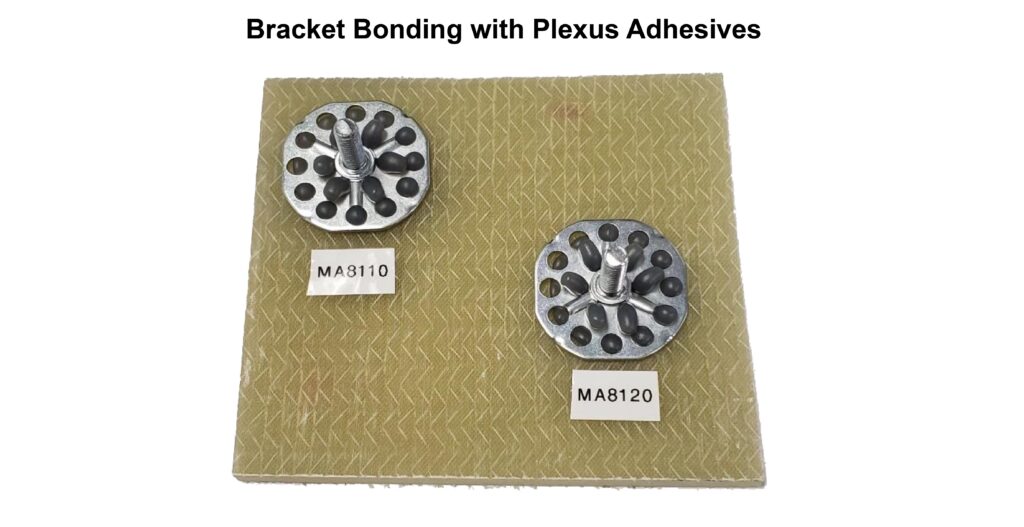
CLAMPING
- Only 0.75PSI – 1.75PSI clamp pressure is needed to spread out most Plexus Products
- For flat sections, bar clamps help provide even pressure
- Mechanical fasteners can be used as clamps to help move products down line faster
- Certain plexus products contain glass beads to prevent excess squeeze out
- Engineered standoffs or gaps can help contain the adhesive and guarantee certain bond gaps
BOND LINE READ THROUGH (PRINT THROUGH)
As adhesives cure they produce heat (exotherm) and shrink. This can lead to a visible area on Class A surface. This is more prevalent on thin materials.
Reducing adhesive print through can be achieved by the follow tips:
- Reduce bond gap – By lowering the bond gap (0.01” to 0.03”), there is less mass of adhesive, less heat and less volume to shrink
- Remove excess squeeze out – less material to heat up and shrink
- Look at a low shrink and low exotherm product – Plexus has specific formulas with reduced exotherm and lower shrink values
Contact Customer Service to learn more about Plexus adhesive solutions most suited for your project.
SURFACE PREPARATIONS FOR ADHESIVES
- Thermoplastics – A simple wipe (to remove any dust) is sufficient in most cases
- Composites – Depends on the chemistry; many RTM, and traditional resin composites can be bonded after a dry rag wipe or light solvent wipe to remove any excess shop dust. Other composites may need light abrading
- Raw Metal – Plexus has a line of primer-less to metal adhesives, which can often bond with no surface preparation or as little as a solvent wipe. For a heavily oxidized metal, surface abrasion followed with solvent wipe is typically recommended
- Coated Metals – Can often be bonded as is, or after a wipe to remove any excess dust.
Testing the exact material being bonded is important to any successful project. If you have a question about your material or your specific project, please reach out to our Technical Service Department.