JOINING AND SEALING WITH PLEXUS ADHESIVES
APPLICATION OVERVIEW
An optimal way to improve manufacturing or assembly productivity is to combine two steps into one. Riveting, bolting or stitch welding are examples of “traditional” joining methods that often require a secondary sealing step. Plexus structural adhesives offer manufacturers the ability to effectively combine the joining and sealing steps.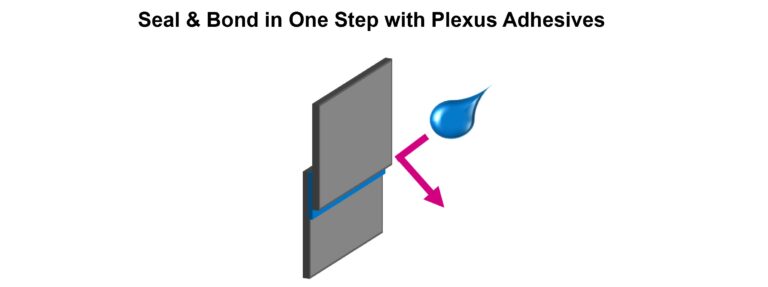
Below is a case study where a manufacturer changed their assembly process and design from a riveted roof assembly to one made with Plexus structural adhesive. Not only was the assembly with Plexus stronger and more durable, but it also saved significant manufacturing time, reduced the units mass and improved aesthetics.
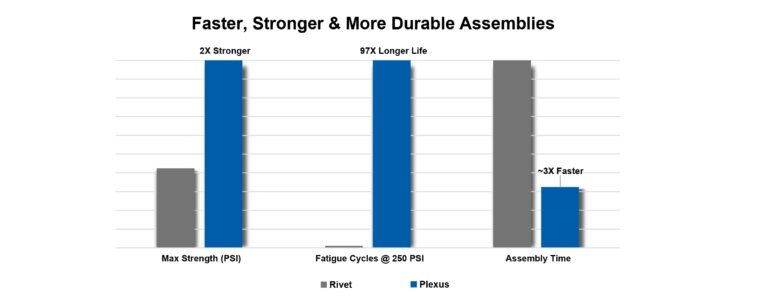
CLAMPING
- Only 0.75PSI – 1.75PSI clamp pressure is needed to spread out most Plexus products
- For flat sections, bar clamps help provide even pressure
- Mechanical fasteners can be used as clamps to help move products down line faster
- Certain Plexus products contain glass beads to prevent excess squeeze out
- Engineered standoffs or gaps can help contain the adhesive and guarantee certain bond gaps
COLOR
Generally, sufficient clamping is recommended to ensure the part is in its proper position with an adhesive gap such that you can see a small amount of squeeze out on the edge of the bonded joint. Depending on the visibility of the joint, some end users then simply use an edger of some sort and create a smooth filet on the joint edge, as they do with a traditional sealant, and some simply leave it as is.
Such a process of creating a small squeeze out of adhesive typically helps to ensure enough adhesive is used to join and seal. Select Plexus products are available in white, black and gray if the exposed seam color is important. If the Plexus color is not suitable, many of the Plexus products readily accept paint, although testing will have to be done to guarantee long term paint performance on Plexus.
SURFACE PREPARATIONS FOR ADHESIVES
Plexus adhesives are engineered to be very robust with minimal or no surface preparations.- Thermoplastics – A simple wipe (to remove any dust) is sufficient in most cases
- Composites – Depends on the chemistry; many RTM and traditional resin composites can be bonded after a dry rag wipe or light solvent wipe to remove any excess shop dust. Other composites may need light abrading
- Raw Metal – Plexus has a line of primer-less to metal adhesives, which can often bond with no surface preparation or as little as a solvent wipe. For a heavily oxidized metal, surface abrasion followed with solvent wipe is typically recommended
- Coated Metals – Can often be bonded as is, or after a wipe to remove any excess dust