PANEL BONDING WITH PLEXUS ADHESIVES
APPLICATION OVERVIEW
A common method of panel construction is a metal frame (almost like a reinforcement skeleton) with the addition of thin panels fastened to that structural frame. Firetrucks, cargo trailers, ambulances, some HVAC, and buses are all examples of that build style. One part or single part systems such as Polyurethanes and Silane Modified Polymers (1K and 1K SMP’s) are sometimes used, however they have a moderate upper limit to the strength they provide and slow cure speeds, often leading manufacturers to look at two component panel glue systems from Plexus that have a higher strength or a consistent and predictable cure rate.COMPOSITE PANELS
Plexus is one of the leading choices for composite glue, since Plexus adhesives have primer-less adhesion and little to no surface preparation to most composites. When bonding composites to steel, aluminum or coated metals, Plexus adhesives are designed to have the right blend of strength and elongation to handle the various levels of thermal expansion between parts. Plexus adhesives also have proven resilient to long-term dynamic fatigue. Structural adhesives can eliminate potential stress cracks or catastrophic failures that rivets or other mechanical fasteners might cause on the panels.THERMOPLASTICS PANELS
Most applicators bonding thermoplastics such as ABS, PVC and Nylon look for adhesives that require little to no surface preparation. Plexus adhesives provide robust adhesion to most thermoplastics and in most cases, fuse to them with no surface preparation.
RAW METAL PANELS
Metal bonding adhesives can often be dispensed significantly faster than welding or riveting, leading to significant production gains. Plexus adhesives provide such benefits as well as they distribute stress over a greater surface area than stitch welds, spot welds or rivets. As a result, many manufacturers look to Plexus as their metal glue of choice.
For more information on Plexus adhesives for metal bonding, see our all the benefits on our Metal to Metal Bonding Page.
COATED METAL PANELS & BRACKETS
There are many advantages in using Plexus adhesives to bond brackets to coated metals. Plexus is non-conductive and unlike mechanical fasteners, it does not need holes in the coated material. This means that Plexus adhesives provide an additional layer of corrosion control and reduce or eliminate galvanic corrosion. Furthermore, Plexus adhesives distribute the stress uniformly which puts less stress on the coating itself, leading to a longer part life expectancy and improved durability.
EXAMPLE OF PANEL BONDING (SHEET TO POST)
STEP 1
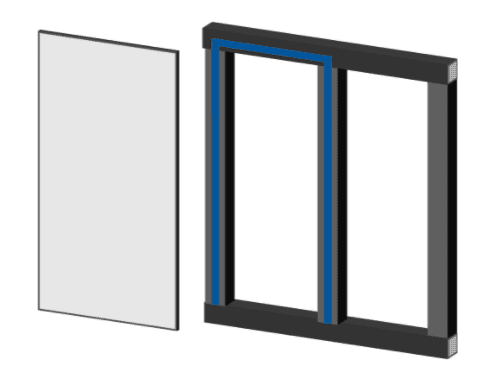
STEP 2
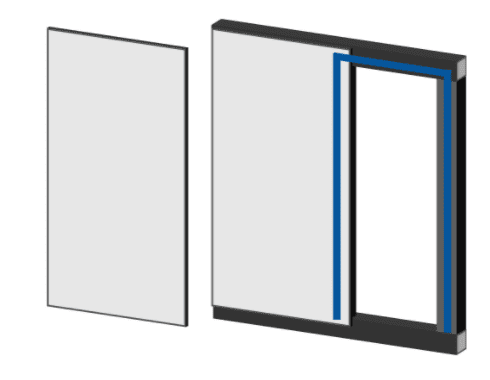
STEP 3
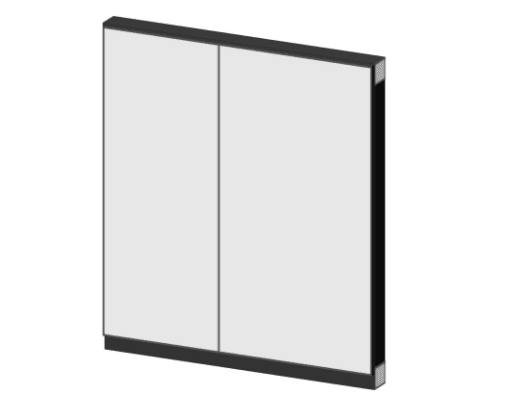
CLAMPING
Plexus adhesives are engineered to be thixotropic so they dispense and spread within a joint very easily. The recommended best practice for clamping on all parts is to ensure an even clamp pressure across the bondline.
Here are some tips for effective clamping during the fixture period:
- Only 0.75PSI – 1.75PSI clamp pressure is needed to spread out most Plexus Products
- For flat sections, bar clamps help provide even pressure across the bond area
- Strategically placed mechanical fasteners can be used to help move products down line faster
- Select Plexus products contain glass beads to prevent over clamping and excess squeeze out
- Engineered standoffs or gaps directly on the part, can help contain the adhesive and guarantee certain bond gaps
BOND LINE READ THROUGH (PRINT THROUGH)
Print through is complicated and includes many influences. Excess pressure on temporary clamping is one factor. Two-part systems can create heat during their reaction and shrink as they cool. This can lead to a visible area on the surface. Read through can be minimized or eliminated by balancing the things that influence it.
Tips to reduce print through:
- Reduce bond gap – By lowering the bond gap (0.01” to 0.03”), there is less mass of adhesive, less heat and less volume to shrink
- Remove excess squeeze out – Less material to heat up and shrink
Contact Customer Service to learn more about Plexus adhesive solutions most suited for your project.
SURFACE PREPARATIONS FOR ADHESIVES
Plexus adhesives are engineered to be very robust with either no or minimal surface preparation.
- Thermoplastics – A simple dry rag wipe (to remove any dust) is sufficient in most cases
- Composites – Depends on the chemistry, most RTM composites can be bonded after a dry rag wipe or solvent wipe. Other composites might need light abrading
- Raw Metal – Plexus has a line of primer free metal adhesives, which can often bond after a solvent wipe. For heavily oxidized metal, abrasion and solvent wipe is recommended
- Coated Metals – Can often be bonded as is after a wipe to remove any dust
Have a question about your material, please contact our Technical Service Department.