REINFORCEMENT BONDING WITH PLEXUS ADHESIVES
APPLICATION OVERVIEW
Certain manufacturing methods are limited in their freedom of design to create complex 3D shapes with integrated ribs or stiffeners. Plastic thermoforming, metal stamping, sheet metal bending and compression molding are some examples of those manufacturing methods that benefit from a secondary step of adding reinforcements.
Plexus has long been one of the leading choices for composite glue, since most Plexus adhesives require little to no surface preparation. Composite to composite bonding for reinforcements is common, as well as using Plexus as a metal to composite glue.
Thermoplastics can be joined by ultrasonic or vibration welding, but that often requires expensive capital investment, may lead to stress cracking and higher variation in dimensional tolerances and limited shape design. Using Plexus adhesives as a permanent thermoplastic glue to bond for reinforcements is a natural choice that leads to long term static and dynamic durability, fast production in addition to a flexible manufacturing site. As with composites, Plexus also bonds mixed materials such as metal to thermoplastics.
Sheet metal has traditionally been thought as required to be welded or riveted, but Plexus structural adhesives for bonding metal have been further enhanced to bond a wider range of metals and coatings. Metal bonding adhesives can often be dispensed significantly faster than welding or riveting, leading to significant production gains. Plexus adhesives distribute stress over a greater surface area than stitch welds, spot welds or rivets.
For more information on Plexus adhesives for metal bonding, please visit our Metal to Metal Bonding Page.
TYPICAL REINFORCING SHEET METAL WITH BONDED HAT SECTION
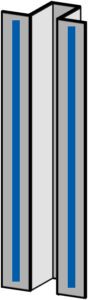
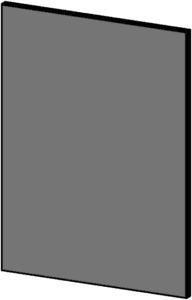
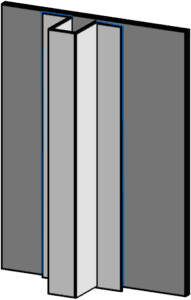
FIXTURING DURING CURE
Plexus adhesives are engineered to not only be thixotropic (non-sag), but also to spread very easily. Best practice is to ensure even clamp pressure across the bondline that is sufficient to prevent joint separation until a defined handling strength is achieved.
Here are some tips for such clamping:
- Only 0.75 psi – 1.75 psi pressure is needed to spread out most Plexus products
- For flat sections, bar clamps help provide even pressure across the bond area
- Mechanical fasteners strategically placed can be used to help move products faster down the production line
- Select Plexus products contain glass beads to prevent over clamping
- Engineered standoffs or gaps directly on the part can help contain the adhesive and guarantee certain bond gaps
BOND LINE READ THROUGH (PRINT THROUGH)
Print through is complicated and includes many influences. Excess pressure on temporary clamping is one factor. Two-part systems can create heat during their reaction and shrink as they cool. This can lead to a visible area on the surface. Read through can be minimized or eliminated by balancing the things that influence it.
Tips to reduce print through:
- Reduce bond gap – By lowering the bond gap (0.01” to 0.03”), there is less mass of adhesive, less heat and less volume to shrink
- Remove excess squeeze out – Less material to heat up and shrink
Contact Customer Service to learn more about Plexus adhesive solutions most suited for your project.
SURFACE PREPARATIONS FOR ADHESIVES
- Thermoplastics – A simple dry rag wipe (to remove any dust) is sufficient in most cases
- Composites – Depends on the chemistry, most RTM composites can be bonded after a dry rag wipe or solvent wipe. Other composites might need light abrading
- Raw Metal – Plexus has a line of primer free metal adhesives, which can often bond after a solvent wipe. For heavily oxidized metal, abrasion and solvent wipe is recommended
- Coated Metals – Can often be bonded as is after a wipe to remove any dust
Have a question about your material, please contact our Technical Service Department.