Illinois State University Solar Car team is managed by students with the goal of learning real-world, problem-solving skills. The training the students receive to research, source, and manufacture solar vehicles extends to teaching students project management, logistics and critical thinking skills. Driving three continual days cross country, with grueling inspections and focused racing resulted in 15 hour work days of continual performance. Naturally, high quality, reliable materials are needed to support the team’s dedication, passion and efforts.
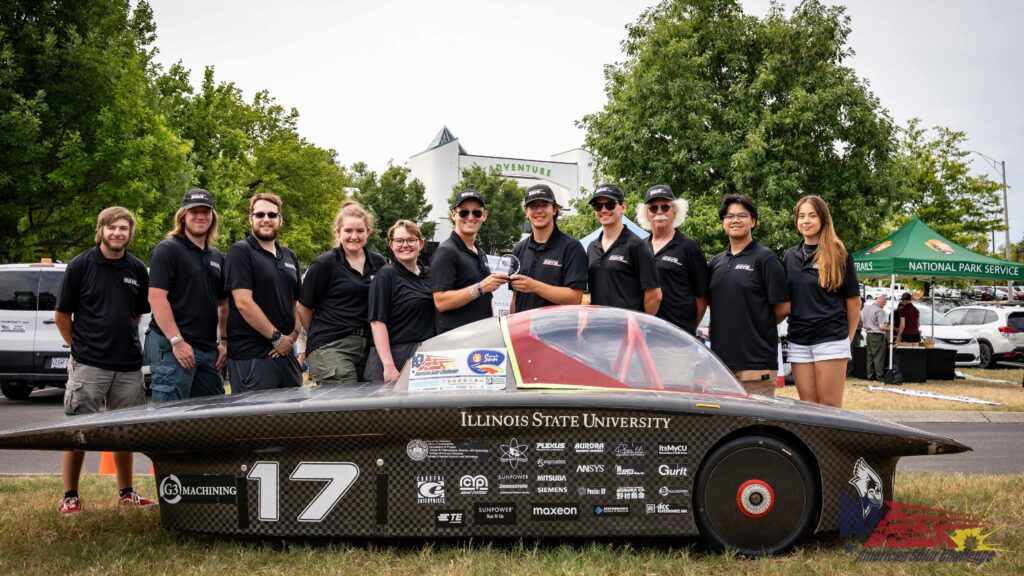
ITW Performance Polymers recognizes the value in supporting our future engineers, designers and other critical studies and has worked with the Illinois State University Solar Car team on three solar cars now. The whole car was constructed of foam (the core material) covered with epoxy impregnated carbon fiber. All individual components were joined together using Plexus acrylic adhesives. The Solar Car Team Advisor, Jim Dunham stated, “Anywhere the composites were used, we joined with Plexus adhesives because we needed a high quality industrial adhesive. All the parts that we designed to be bonded in the secondary operation of manufacturing, were bonded with Plexus. At this point in the process, the carbon fiber has a very fine, rough surface that further helps the adhesive interlock and fuse to the carbon epoxy matrix without any further preparation. If the part has been out for long, the assemblers wipe it with acetone. But right out of the mold, it can be bonded.”
Dunham further explained that, “An epoxy wouldn’t work here. Plexus adhesives are thicker and fill small voids. The rails of the vehicle aligned with the body but there were small gaps. The Plexus brand of adhesives bridges those gaps and increased the bonding strength. It would be nearly impossible to get the same level of strength from an epoxy, especially a thin epoxy. We needed a grown-up strength adhesive.”
As with the previous vehicles manufactured, the team wanted to use a multi-material product that wasn’t limited to being only a metal to metal adhesive as aluminum inserts and body panels needed bonding. Plexus MA8110 and Plexus MA310 adhesives “worked well with both the aluminum and the carbon fiber. In addition to being the right glue, they needed a quick cure because we didn’t have the time to clamp something for long periods of time. As you can imagine, this has come in handy over the years for emergency repairs. We even brought the Plexus adhesives with us during the race, as a result.”
A reliable adhesive, its adhesion strength and overall performance was critical for the small, student-led team, apt to seeing equipment break on these types of solar cars. With over 30 teams showing up to the race, 25 made it onto the track. “These vehicles need to be rock solid and safe for public roads,” said Dunham. “There are thorough inspections (mechanical and electrical) that are strict. These vehicles cannot be thrown together as they share the road with other public vehicles, going through cities and towns. This route went straight through the center of Kansas City. On a road race, a three-car caravan is driven, so safety is key.” Because the Plexus brand of adhesives has a successful track record of bonding not just these solar cars but well-known OEM brands of consumer and commercial automobiles, the Illinois State University Solar Car team knew they had the reliability they needed.
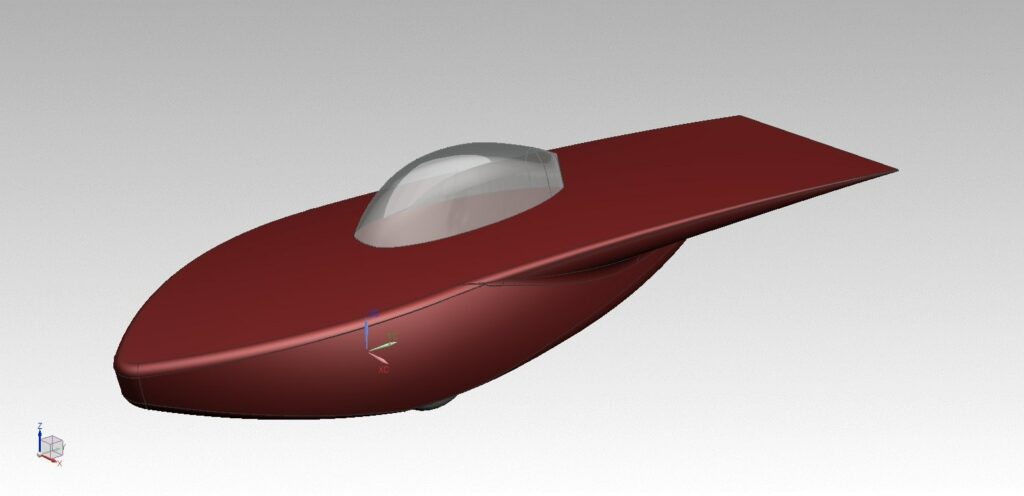
During the three days of inspection, which included intensive performance on dynamic courses, the testing was, “Very thorough where it’s not unusual for solar vehicles to fail. The engineering report that shows strength analysis accompanied the dynamic course for proof of safety, performance, and structural soundness to go on public roads,” explained Dunham.
The outcomes were measurable. In addition to quality adhesion, gaps being filled, and “the incredibly strong and reliable bond,” Dunham says driving 50 mph down county rounds and hitting potholes didn’t break the suspension. The Illinois State University Solar Car team placed third at the Formula Sun Grand Prix. To place, the team raced for three days on the 3.15 mile track, eight hours each day as the car completing the most laps during that time in the winner. The Illinois State University Solar Car team completed 149 laps (469 miles), beating five “Big 10” teams.
During the American Solar Challenge Road Race, the team found more success placing third there as well. Starting in Nashville, TN and arriving in Casper, Wyoming, they drove 1,600 miles in eight days. This achievement was extra special for the team as this was the first time they completed the entire route without having to trailer the car. ITW Performance Polymers is proud of its Plexus brand and is thrilled for the students, their impressive hard work, success and as future leaders.