IMPROVE MANUFACTURING THROUGHPUT WITH PLEXUS ADHESIVES
OPTIMIZE ASSEMBLY PROCESS & PRODUCTION THROUGHPUT
After unplanned or forced shutdowns due to unforeseen events, manufacturers often must reconcile with a large backlog of orders. This is where Plexus methylmethacrylate adhesives are proven to assist OEMs with their manufacturing efficiency. Plexus adhesives have a long history of performance and are designed to optimize manufacturing processes and improve production throughput.
We target ways to reduce the amount of labor, Before joining parts, During the joining process, and After the joining process.
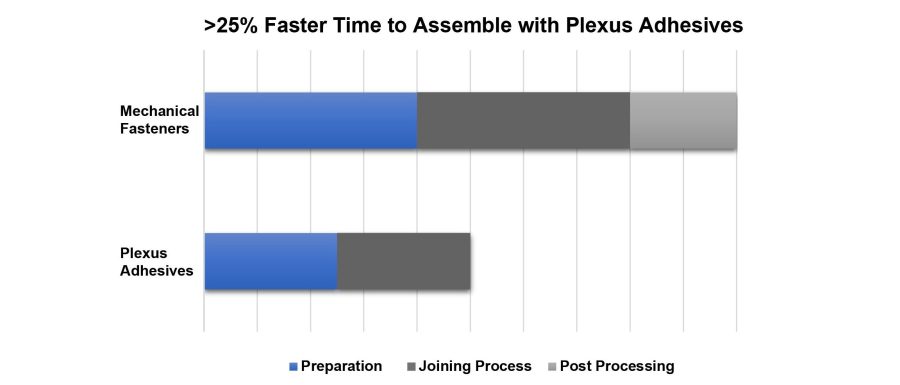
UPSTREAM – BEFORE THE JOINING PROCESS
Reduced Preparation Steps: Select Plexus adhesives are primer-less, adhering to many substrates, eliminating time consuming and costly surface preparation steps.
Many substrates require only a dust free surface or light solvent wipe, which preserves the original substrates intended surface. No holes need to be pre-dilled or punched. No rivets have to be placed.
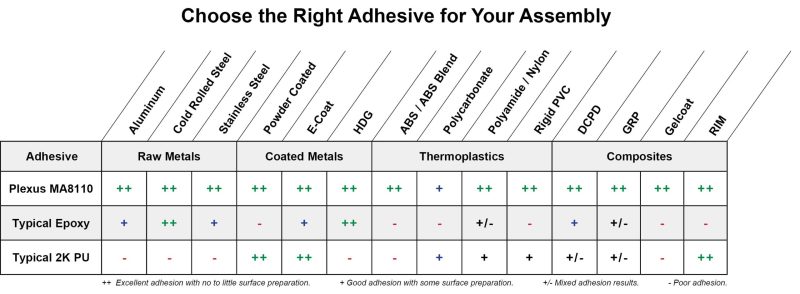
DURING THE JOINING PROCESS
Fast dispensing and quick curing mechanisms are some key attributes that contribute to faster production times. This is seen in the following case study; When joining a hat section reinforcement to sheet metal, Plexus can be seen to use the least amount of labor to complete the assembly:
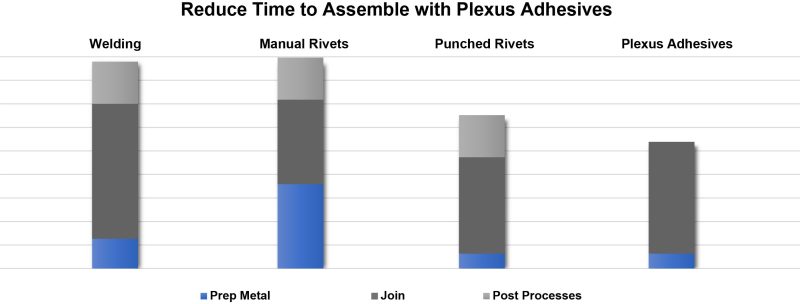
Plexus adhesives exhibit fast strength development. Compared to other adhesive chemistries, Plexus systems achieve rapid fixturing strengths allowing for less waiting and the ability to unclamp much quicker. This results in a more flexible manufacturing environment with fewer fixtures.
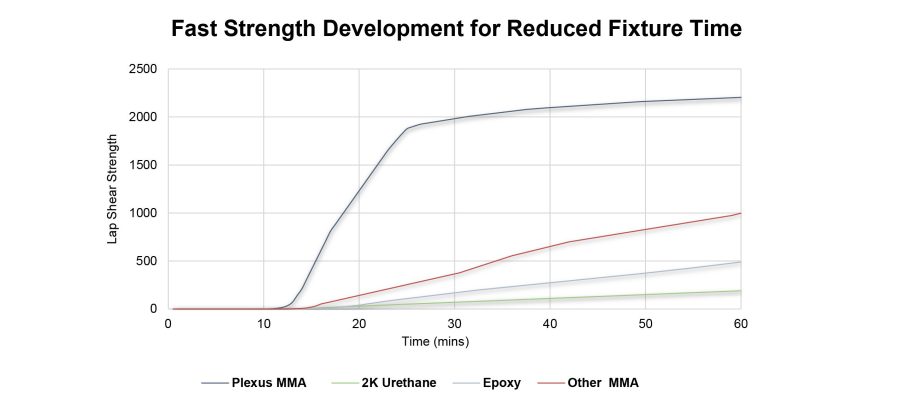
DOWNSTREAM – AFTER JOINING STEPS
Plexus adhesives structurally join and seal parts. This often eliminates secondary sealing steps, which takes more time and added costs. The area where sealant is applied could be in another part of the plant or a different equipment may be required. Moving parts throughout the plant or changing equipment further contributes to wasted time and added assembly costs. Such a scenario is common.
Below case study demonstrates the use of Plexus adhesives to replace manual riveting of a large roof section, which included a secondary sealing and finishing step. Results show assembly time (man-hours) was reduced by 1/3rd when joined using Plexus adhesives.
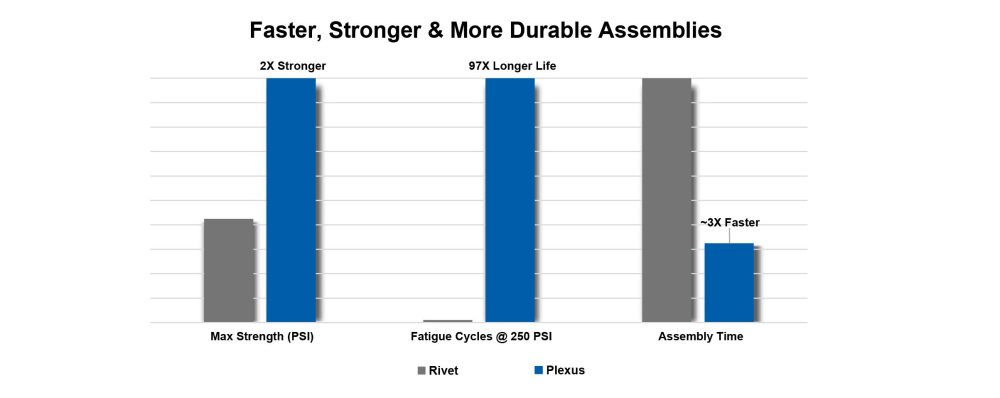
Another downstream step that can be reduced (especially when switching from welding), is the reduction in grinding or realignment due to warping. Plexus adhesives can be an incredibly strong metal glue used to replace welding. Eliminating warping due to excess heat generation and eliminating grinding downstream are the key reasons manufacturers switch to Plexus Adhesives.
To learn more about Plexus products, Contact our Technical Service Department Today!
SEE HOW EASY IT IS TO APPLY PLEXUS ADHESIVES
Seeing is believing. Watch this short video to see how easy it is to apply Plexus adhesives.
MAKING THE SWITCH TO PLEXUS ADHESIVES
Before starting metal to metal bonding or using a metal bonding adhesive in general, there are a few important considerations:
I. What metal or other material will be bonded?
II. What surface preparation is required to get a good adhesive bond to metal?
III. How to bond metal with Plexus adhesives?
I. What metal or material will be bonded?
Plexus® Structural adhesives bond a variety of different metals including coated metals:
- Aluminum – Mill Finished
- Mild Steel
- Galvanneal
- Aluminum – Coil Coated
- Hot Dipped Galvanized (HDG)
- Chromate
- Aluminum – Anodized
- Electrogalvanized (EZG)
- Stainless Steel
- Aluminum – Extrusions
- Galvalume
- Magnesium
- E-Coated Metals
- Powder Coated Metals
- Nickel
II. Surface preparation
Several Plexus adhesives including the MA200, MA800, and MA8000 Series can bond metal to metal without a primer. The Plexus MA8000 series can even be used galvanized or zinc coated metal without primer. However, some of the other adhesives in the Plexus portfolio require a Cleaner Conditioner called PC120. PC120 helps to clean the metal surface and improve strength of the bond over time. PC120 is dyed pink so that you can easily see where the metal has been properly cleaned.
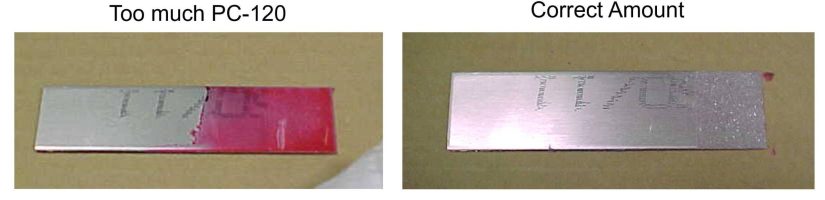
Below is the typical surface preparation required to glue metal to metal:
Surface | Typical Surface Preparation | Typical Surface Preparation |
Type of Metal | Plexus® Primerless Adhesive | Plexus® Adhesive |
Lightly Oxidized Metals | Dry Rag Wipe or Solvent Wipe | PC120 Cleaner Conditioner |
Heavily Oxidized Metals | 1. Solvent Wipe (IPA or Acetone) 2. Sand or Grind 3. Solvent Wipe | 1. Solvent Wipe (IPA or Acetone) 2. Sand or Grind 3. Solvent Wipe |
Coated Metals* | Dry Rag Wipe or Solvent Wipe | Dry Rag Wipe or Solvent Wipe |
*Testing needed to confirm adhesion to different coatings
Salt spray results using PC120 and Correct Amount to Use:
III. How to bond metal with Plexus Adhesives
Plexus adhesives are 2-part (shortened to “2K”) adhesives that create a chemical reaction when mixing. The adhesives are typically mixed in a static mixer and dispensed unto on side. The two materials are mated together and then held in place until the adhesive has had time to cure or harden. This is often done by clamping. The adhesive continues to cure and once it has developed enough strength, the assembly can be unclamped.
Here are some key things to know:
- Working Time (also known as Open Time): The time elapsed between the moment Parts A and B of the adhesive system are combined and thoroughly mixed and the time when the adhesive is no longer useable.
- Fixture Time (also known as unclamp time): The time elapsed between the moment Parts A and B of the adhesive system are combined, thoroughly mixed and parts put together and the time when the assemble can be unclamped. This can change depending on the ambient temperature and temperature of the parts.
- Fixture strength: If the part needs to be lightly moved around, then 50 PSI might be enough strength. If the part will see higher loads after being put together, then 500 or 1000 PSI might be needed. Our Technical Service Department can help provide additional information. Get in touch with our technical service team via the contact form on the right.
BENEFITS OF BONDING METAL TO METAL WITH PLEXUS ADHESIVES
Strength and Durability of Plexus Adhesives on Metal to Metal Bonding
Proper usage of Plexus® Adhesives for bonding metals is expected to have significant advantages over traditional joining methods e.g. rivets, nuts, screws. Gluing a part can be a lot faster and can help speed up most assembly process. The continuous connections, strength and durability of adhesives may help to create a stronger structure than other joining methods.
Bonding Dissimilar Materials with plexus adhesives
Not only does Plexus® adhesives bond metal to metal, they are also often used to bond metal to composites and bond metal to thermoplastics.
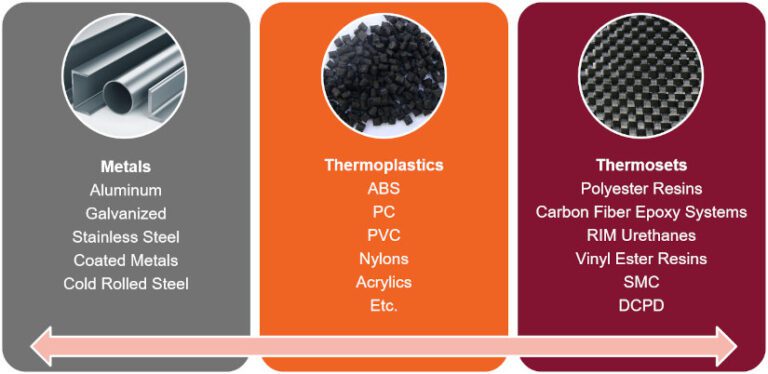
For more information on bonding dissimilar substrates, get in touch with our technical services department via the form on the right.
ADHESIVE SELECTOR GUIDE
Looking to bond certain metal or coated metal? See our adhesive selector guide for full details.
If you have any questions about our adhesives or a project you are working on, please don’t hesitate to contact our technical service team.