
METAL BONDING WITH PLEXUS® ADHESIVES
Plexus structural adhesives have been implemented by various manufacturers to replace rivets, mechanical fasteners, and welding. This page is a great starting point for metal bonding adhesives, but please don’t hesitate to reach out to our Plexus sales and engineering teams for additional advice and insights.
Application Overview
Metals are utilized in a wide range of industries and applications. Metal joining techniques are diverse and varied, but some of the most common are welding (MIG, TIG, and Spot), mechanical fastening (bolts and rivets), and using adhesives. Plexus adhesives make for great metal bonding applications if there is an overlap (sufficient surface area). Some of the most common metal bonding applications are:

Bonding in Reinforcements – Many manufacturing methods benefit from bonding on stiffeners or ribs with Plexus adhesives. Plexus bonds a wide range of materials with little to no surface preparation. The final assembly benefits from the stress distribution, high strength, and elongation that Plexus provides.
Bonding Panels to Frames – Many markets produce products by joining panels to frames. Design engineers like that Plexus joins material substrates. Manufacturing enjoys how easy, non-sag, and fast Plexus is to use. The end results are strong, robust structures.
Bonding on Brackets and Accessories – Plexus is commonly used to bond metal brackets to composite or plastic substrates. Brackets see high levels of stress and therefore benefit from the high strength, elongation, and fatigue resistance that Plexus offers.
Rivet Replacement – Plexus has successfully replaced rivets and other mechanical fasteners in a wide range of applications. Engineers benefit from the stress distribution. Manufacturing loves reducing steps (hole, place, pop, seal) to one step: Bond with Plexus.
Welding Replacement – Plexus has successfully replaced welding for multiple applications. Companies see a huge reduction in time and labor costs, while maintaining strength. Plexus provides distinct advantages when welding thin metal to thick metal, as there are no weld marks, warping, or HAZ.
How To Use Plexus Structural Adhesives To Bond Metal?
Operators using Plexus adhesives for the first time are often surprised by how easy it is to use. Training a new operator can be accomplished in less than 30 minutes. Here is a video showing how to dispense a cartridge of Plexus structural adhesives:
1.) Prepare Surface for Metal Bonding:
All structural adhesives adhere to the outer surface of the two joining materials. Proper surface preparation is critical to ensure a reliable surface for any successful bonding application. Plexus adhesives are designed for primerless adhesion to aluminum and can even cut through some mill or stamping oil. To clean the surface of fresh aluminum with minimal oxidation, use a clean rag and solvent. In the case of heavily oxidized aluminum, or if the part will be exposed to extensive environmental exposure, a solvent wipe is recommended, followed by light abrasion and an additional solvent wipe. Advanced (and expensive) surface conditioning such as acid etching usually not required with Plexus MMA adhesives.
2.) Lightly Abrade Aluminum to Prepare for Metal Bonding
3.) Dispensing Plexus adhesive
Plexus MMA is a two-part adhesive, where the mixing of Part A with Part B starts the chemical reaction. Mixing through a mixing tip (or static mixer) is the best practice. After mixing, the adhesive has a “working time” or “open time” to dispense the adhesive and join the two parts. Open time is affected by temperature – warm temperatures result in shorter work times and cold temperatures extend work times. Dispense rates vary based on the chosen product, the dispenser used, and the mix tip configuration. Plexus adhesives generally dispense very quickly. Most versions of Plexus MMA are non-sag, meaning they do not slip down when applied to vertical surfaces.
4.) Clamping
After dispensing Plexus and joining the two parts, clamp or fixture the assembly until the adhesive cures sufficiently. The amount of adhesive strength required to remove clamps/fixtures depends on the application, size/weight of the parts, and the assembly process. Lighter parts may only require a few pounds (Newtons) of strength, while large assemblies may need more strength and so a longer curing time.
There are several ways to fixture parts as the Plexus adhesive cures. C-clamps or custom-built clamp systems are standard methods for holding assemblies in place. As mentioned, hybrid joining with fasteners used as a clamp is another option. Apply uniform pressure to help wet out the MMA adhesive to a predetermined bond line thickness.
5.) Curing
Plexus MMA adhesives cure via a free radical reaction, building strength quickly at room temperature. Cure rates are affected by ambient temperature, but not humidity. Heat accelerates curing, but there is a recommended maximum threshold for heating MMA adhesives (typically around 150°F or 65°C). Full cure can take a day to a week at room temperature, but only a portion of the complete cure is required to finish the assembly for the majority of applications.
Additionally, the reactivity of Plexus adhesives can be adjusted by changing the mix ratio. Most formulas can accept ±20% off-ratio, and some 1:1 Plexus formulas will accept even greater off-ratio mixing. Please consult with the technical service team at ITW Performance Polymers to help answer any additional questions around Plexus curing.
Key Primerless to Metal Adhesives:
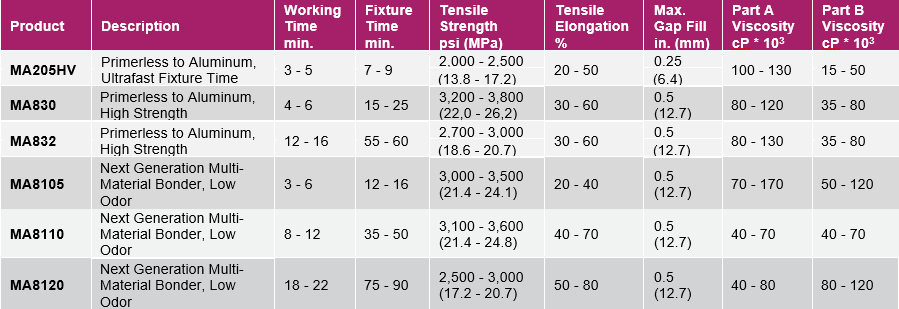
To select a Plexus structural adhesive, we must make sure the adhesive fully bonds with and is compatible with the substrates. The next factor to consider is “open-time,” or the time needed to dispense the adhesive and fit the parts together. Other considerations include the gap-filling capability and cross-bond compatibility of the adhesive with other materials. The Plexus sales and engineering teams can help focus the adhesive selection and provide additional insight.
Why Adhesives Compared To Welding?
Plexus structural adhesives currently replace welding in many structural applications. There are a couple of main driving factors for this, highlighted below:
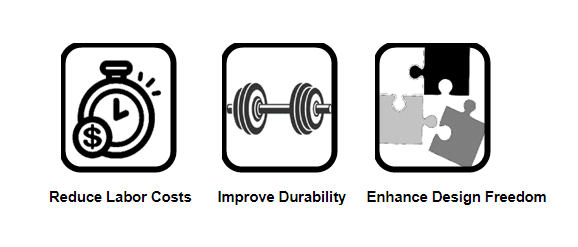
Reduce Labor Costs – Lowering costs is a principal driver for switching from welding to adhesives. Welding requires highly specialized training, and it can be very hard to find and retain good welding talent. The switch from a weld to an adhesive bond offers additional labor savings. For example, Plexus adhesives eliminate the need to grind down weld marks or fix heat distortion on the parts.
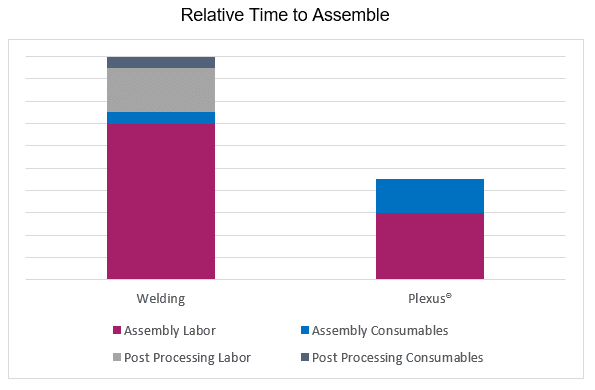
Improve Durability – Plexus stronger-than-weld adhesives outperform a welded joint in some cases. Achieving this depends on the material being bonded and the size of the joint. The switch from weld to adhesive pays off, especially because you can use the adhesive to join a larger surface area, distributing stress. Additionally, Plexus does not create heat-affected zones (or “HAZ”). Eliminating HAZ makes the entire metal structure stronger. In some cases, the HAZ is the weakest link in the design so replacing the weld with adhesive allows our customers to downgauge their metal and simultaneously create a more robust structure.
Enhance Design Freedom – A key benefit of using Plexus adhesives is they are not only primerless to metal, they are also primerless to composites, most plastics, and coatings. The ability to bond multiple materials allows design engineers to join dissimilar metals without galvanic corrosion, or to incorporate a multi-material design. Metal to metal bonding also comes with specific design options. Welding can cause warping or burn through when joining thin gauge metal to thicker metal. Plexus adhesives eliminate weld burn through and can enable thin to thick gauge joining. Areas that are difficult to access with a welder can be easily bondable.
When Not to Use Adhesives to Replace Welding
Incompatible joint design that cannot be changed – Adhesives should not always be used as a drop-in replacement for welding. Some joint designs, like butt joints, are incompatible with adhesives.
Continuous high-temperature exposure – Structural adhesives are primarily organic polymers that soften when exposed to heat, limiting their usage in specification applications exposed to continuous high heat (>250°F or 121°C).
Large welds on thick plate metal – Very thick welds on thick metal (>0.375″ or 9.5mm) will usually have a structural strength that is difficult for most adhesives to match. Most weld replacement with metal glues happens when one weld thickness is below 0.30” or 7.6mm.
Continuous exposure to incompatible chemicals – Adhesives are made of organic polymers. Although they can withstand common environmental exposures like saltwater, cleaning products, etc., they may not stand up to repeated exposure or complete immersion with certain chemicals. When in doubt, contact Technical Services for answers.
How To Replace Welding With Plexus?
A couple of critical considerations when converting from welding to adhesives:
Force & Stress – How much stress will the parts be exposed to, and what type of force? If the amount of force a welded joint can accept before failure is known, our Technical Services can provide typical shear strengths possible with Plexus adhesives for various metals. Then the area of adhesive coverage necessary to be more robust than the weld can be calculated.
Environmental Considerations – What environmental conditions, such as temperature, humidity, weathering, will the assembly endure? What is the expected life cycle of the assembly?
Workflow – How will switching from welding to adhesive bonding change my manufacturing workflow?
Design – What is the joint configuration? Joints designed for structural adhesives require overlap. However, metal inert gas (MIG) or tungsten inert gas (TIG) can get away with fewer contact points/areas. Weld geometries that require a design change are butt, mitre, and “T” joints. Below are typical weld joints converted to adhesive-friendly configurations.
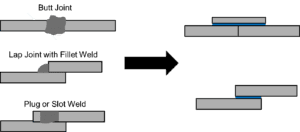
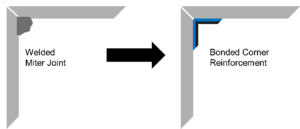
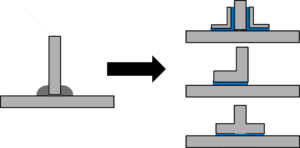
Riveting and welding aluminum provide instant fixture, while adhesives require time to cure enough to remove fixtures. However, Plexus adhesives dispense quickly and can be applied 10 – 20 times faster than welding. Aligning the workflow so that one set of parts finishes its fixture time simultaneously with the time needed to dispense, join, and clamp the second set of parts. This optimization results in highly efficient workflows (doubling the efficiency in the same overall time as welding).
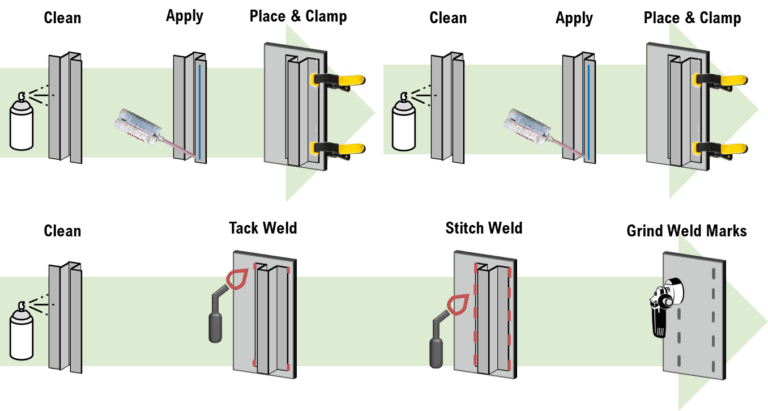
Why Plexus Adhesives Compared To Rivets Or Mechanical Fasteners?
Plexus structural adhesives are being used as a rivet replacement by numerous manufacturers for a variety of reasons:
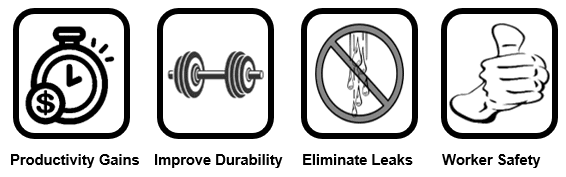
Productivity Gains – Riveting is a multi-step process requiring additional sealing steps. Switching to Plexus adhesives eliminates drilling holes and subsequent sealing steps.
Improve Durability – Rivets and bolted assemblies act as stress concentrators, whereas plexus adhesives distribute stress. As a result, Plexus adhesives have much higher shear and tensile strengths as well as long-term durability. Additionally, durability tests correlate with fatigue resistance, where Plexus adhesives typically perform 100 – 1,000 times longer than riveted assemblies.
Eliminate Leaks – Adhesives require no holes. Instead, they bond and seal at the same time. Eliminating holes dramatically reduces the chance of leaks. For example, a study of bonded insulated panels vs. riveted + sealing gaskets showed the Plexus adhesive bonded panel absorbed 6 times less moisture when exposed to accelerated salt-fog aging.
Worker Safety – Drilling and “popping” rivets can be dangerous for workers. If their attention wanders, it could cause a pinch point. Drilling and riveting can also be quite loud and damaging to workers’ hearing. After switching to Plexus adhesives, one manufacturer could not believe how quiet their operations became. It was possible to hold a conversation on their shop floor and they did not need hearing protection.
How To Replace Rivets Or Mechanical Fasteners With Plexus Adhesives?
Compared with welding, converting from rivets to Plexus adhesives is more straightforward. Most blind rivets come with documented shear strength. Most Plexus products are significantly stronger than the rivet shear strength and join more surface area, efficiently distributing stress and enhancing assembly durability and performance.
Contacting our sales engineers is an easy way to convert from rivets to adhesive. We can audit your design and assembly process to make adhesive recommendations. Usually very few or no design changes are required to replace fasteners with adhesives.
Hybrid joining can be an easy option to ease into adhesive bonding. In this case, it is defined as using both rivets and adhesive to join two parts together. Typically, a fastener is used at key points to hold the part together as the adhesive is curing.
Design Recommendations For Structural Adhesives
When designing assemblies for Plexus adhesives, there are a few best practices and things to keep in mind.
Surface Area – Bond length has a more significant effect than bondline overlap. Therefore, when possible, maximize bond length and use enough overlap to achieve the necessary strength after considering safety factors and potential limitations of shear strength from external effects like temperature.
Gap Management – Adhesives tend to be the strongest within a certain thickness range. For most Plexus products we recommend a 0.01” to 0.03” (0.25 – 0.75mm) gap for metal bonding. Adding measures like stand-offs into the part design can help operators locate where to place the adhesive and ensure reliable, consistent gaps.
Stress Considerations – Adhesives are best in shear and tension. Joint designs should minimize peel and cleavage force. If it is impossible to avoid high peel forces, consider a combination of adhesive and fastener.
Tests And Verification Of Metal Bonding Adhesives
Plexus has a fully equipped test lab to verify adhesive performance on a wide variety of substrates. Lab tests typically use small-scale coupons of substrates. Larger scale prototypes and durability tests are typically done at the manufacturer, based on the manufacturers’ internal test methods.
Lap Shear
Adhesive lap shear testing via ASTM D1002 determines the strength of an adhesive bond under shear loading. ASTM D1002 is an industry standard test that allows adhesive performance to be compared side-by-side for strength and bond failure modes. Bonded test coupons are loaded into a testing frame and pulled at a standard rate.
Environmental Exposure
The ITW Performance Polymers Technical Services laboratory can perform long-term environmental tests to replicate real-world product performance. Capabilities include salt fog, humidity, and temperature testing, simulating exposure to the specific climate that a product will experience.
Cross Peel
Adhesive Cross Peel testing via SAE J1553 evaluates the strength of an adhesive bond when loaded with a perpendicular peel force. Many real-world adhesive joints, including stringer-to-hull bonds in boatbuilding, experience these kinds of peel forces. Cross Peel testing allows manufacturers to simulate real-world peel loadings on bonded parts and investigate potential failure modes.
Impact Resistance
GM9751P Side Impact testing determines the strength of an adhesive bond when under impact force. Impact testing is beneficial to understand bond strength and failure modes in the event of a collision or worst-case scenario.
Testing the exact material you are bonding is important to any successful project. Contact our Technical Services Department to learn more on how Plexus adhesives can help you bond better.
Why Partner With Plexus Adhesives?
Plexus structural MMA adhesives have a long history of providing durable structural bonds to metal substrates. These advanced adhesives have been qualified under rigorous automotive & transportation specifications & performance requirements and have a long history of success in the field. In addition, our primerless to metal adhesives (sometimes called metal glue) are capable of the harshest environmental & service conditions with minimal or no surface preparation.
Value Add Services to the Customer
- Application Knowledge – Providing technical information and insight to answer engineering and processing questions for our customers.
- Technical Support from ideation to production – Focused support with product experience to help assist with product related questions that help customers with existing and new projects.
- Local Resources – Local sales managers are strategically located and available to provide fast, professional expertise, and supported by a vast distributor network with local inventory.
- Guaranteed quality certified ISO 9001.
Technical Capacity:
- Our Technical Service Lab is fully equipped for application and product testing.
- Team of Technical Service Engineers to help answer questions, problem solve, and test our industrial strength adhesives on various materials including plastics bonding systems.