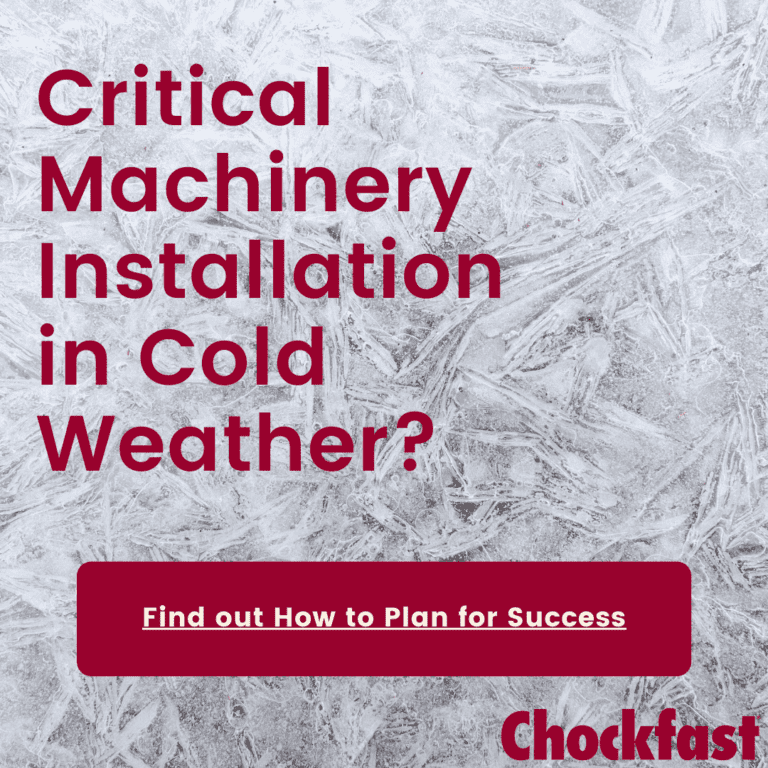
This is the first of a series of posts that will cover the best recommendations and keys to achieving successful installations of critical equipment using precision epoxy grouts and epoxy chocks, also known as non-shrink epoxy grouts and chocks, in cold weather conditions. This series includes three articles:
- This post will focus on why epoxy grouts and epoxy chocks have a minimum application temperature and why it is imperative to stay above this temperature throughout the installation and initial curing cycle of the material.
- The second post will discuss the effects that cold temperatures have on the physical properties of non-shrink epoxy grouts and chocks when exposed to cold ambient temperatures.
- The final post will discuss the specific recommendations for achieving a successful installation of Chockfast epoxy grouts and chocks in colder ambient temperatures.
Why Precise Temperature of Epoxy Grout Matters for Foundations
A wise man once said that there are, on average, 2 perfect days every year for installing non-shrink epoxy grouts and chocks where the temperatures are maintained in the right range, there is no threat of precipitation, and the epoxy grout installation area is protected from direct sun exposure. Planning a successful installation must assume that it will occur on one of the other 363 days that require at least some consideration to ensuring that all material components and the foundation is within the recommended application temperature range, which can be easily found in the specific Product Data Sheets.
Without proper planning and consideration, the costs and on-site complexity associated with conditioning an effective foundation system in pipelines, chemical refineries, mining operations or other critical industrial operations, especially in cold ambient temperatures, can be unexpected and affect the feasibility and profitability of achieving a long-term installation of reliably operating critical equipment. This is especially a concern as more and more projects are awarded to low bidders, which may often overlook or leave out this vital step. By properly understanding the minimum application temperature and considering the effects that cold temperatures have on the physical properties of precision epoxy grouts and epoxy chocks, there is a profound increase in the probability and ease of achieving a successful installation of an effective foundation system.
Is it truly necessary to keep an epoxy grout above 55°F (13°C) during installation?
Yes. When reviewing the product data for just about any precision epoxy grout and epoxy chock, you’ll find a typical temperature range. While there is often variation on the maximum recommended application temperature, most products will publish a minimum application temperature of around 55°F (13°C). This is the most commonly published minimum application temperature of all epoxy-based products, not just non-shrink epoxy grouts and epoxy chocks, because this is near the temperature where the chemical reaction of epoxies will essentially “shut down.”
While the chemical reaction doesn’t turn off like a switch, it does slow down substantially. Here are some potential signs that an installation of precision epoxy grouts or chocks may have dropped below the critical minimum temperature:
- Material does not transition from a liquid to a solid after more than 24 hours
- Material does not reach the design strength within the time published in the technical data sheet
- Material does not reach the intended Barcol Hardness within the time published in the technical data sheet
Can I “restart” the chemical reaction if the temperature unexpectedly drops below the minimum application temperature?
Not effectively. While the chemical reaction can be typically be “woken up,” or reinitiated, by heating the entire foundation area above 80°F (27°C), research has shown that the epoxies will not achieve the same ultimate physical strength properties as materials that maintained temperatures above the minimum application temperature.
The decrease in the ultimate physical properties of the material is largely due to the decreased glass transition temperature. Because the energy of the chemical reaction between the epoxy components (resin and hardener) is being used to heat the material up to the proper reaction temperature range, it doesn’t have the energy required to build the crosslinked chemical bonds that will create the physical structure and high-strength properties expected in epoxy-based products. Testing has shown that 30% or more of the ultimate physical properties of the material may be lost with precision epoxy grouts and chocks that drop below the minimum application temperature during the initial curing of the material.
Do special formulations for applications at lower temperatures work?
Yes, but with precautions. Some products will use special chemical formulations to allow pouring at lower minimum application temperatures by adding more reactive components to the mixing process. While these additives will help to increase the overall reactivity of the formulation and energize the chemical reaction in colder ambient temperatures, there is always a risk of excessive exothermic reactions depending on the actual conditions of the application. Some potential downsides of these additives are:
- More dynamic chemical reactions, which can potentially lead to excessive pulldowns and loss of alignment
- Misuse of cold weather formulations in temperatures over the recommended temperature range in an attempt to speed up the initial cure process, causing more volatile chemical reactions, as highlighted above
Achieving Successful Epoxy Grout Installations in Cold Weather
By understanding why epoxy formulations (especially those used in critical environments such as below dynamic equipment) have a minimum application temperature, installers can better plan for and use epoxies.
Chockfast high-performance epoxy grouting and chocking compounds have provided precise and permanent alignment of all types of dynamic and critical machinery such as major gas pipelines; chemical, petrochemical, and refining complexes; power plants; mining operations; and other worldwide industrial construction operations since 1958. When applied at the appropriate temperatures, the Chockfast System supports more horsepower than any other system on the market. Using the best epoxy grout for your application matters, so pick the right solution for your team.
The next post in this series will discuss the specific effects that colder ambient temperatures have on the physical properties of precision epoxy grouts and chocks.
To further discuss achieving the recommended environmental conditioning for an upcoming installation of precision epoxy grouts or chocks, contact ITW Performance Polymers Technical Services or your local Chockfast Worldwide Distributor Network representative.
View all our Technical Data Sheets and Safety Data Sheets. Need some help? Ask a technical question and find a solution!
Further reading: Cheat Sheet: Chockfast® Epoxy Grout Typical Installation Steps and Laying The Foundation For Success With Chockfast® Epoxy Grouting.
For more stories like this, follow ITW Performance Polymers on LinkedIn and sign up for enewsletter in our website footer.