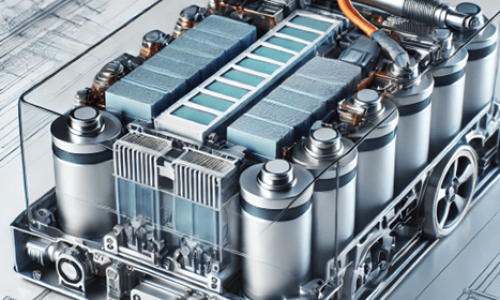
Introduction
Electric vehicles (EVs) are at the forefront of the global transition towards battery charged cars and sustainable transportation. Central to the success of electric cars are their batteries, which are comprised of numerous individual cells assembled into modules and battery pack housing. However, combining all of these components into one, cohesive battery pack has proven to be a complex challenge. This intricate assembly process has been revolutionized by the use of structural adhesives like Plexus MA7020. This adhesive not only enhances the design and durability of electric vehicle battery technologies but also contributes to their overall performance.
Battery Adhesive
Durability
Structural adhesives play a critical role in enhancing the durability and safety of electric vehicle batteries. These battery adhesives provide robust bonding between battery cells, modules, battery pack housing, and covers. Plexus MA7020 is compatible with electric vehicle battery materials like aluminum, E-Coated steel, PET film, nickel coated steel, and nylon. Significantly reducing the risk of mechanical failures caused by vibrations and impacts during vehicle operation.
Thermal Management
Moreover, thermally conductive structural adhesives like Plexus DT2630LD contribute to the thermal management of the EV battery pack by facilitating even distribution of heat, thus preventing hotspots that could lead to thermal runaway incidents. As a result, the use of structural adhesives ensures that the EV battery remain structurally secure, resistant to harsh conditions, and ultimately enhance the safety of the entire vehicle.
Lightweighting – Increased Design Freedom
One of the significant advantages of using structural adhesives in electric vehicle batteries is their contribution to weight reduction. Traditional mechanical fasteners, such as screws and bolts, add unnecessary weight and occupy valuable space within the electric car battery pack. In contrast, ambient cure structural adhesives like Plexus MA7020 offer assembly solutions that involve less processing, takes up less space, and achieves higher strength and durability all while being electrically insulating. This contributes greatly to reducing the overall mass of the electric car battery assembly.
Additionally, battery adhesives provide greater design flexibility by allowing manufacturers to structurally join dissimilar EV battery pack materials like plastics and metals. In these types of dynamic environments, Plexus adhesives offer superior toughness without concerns regarding CTE mismatch, the need for highly skilled labor, or overly complex joint designs that other fastening methods require.
Sustainability
The adoption of structural adhesives in electric vehicle batteries also aligns with the broader goal of increasing efficiency and reducing environmental impact. Structural adhesives facilitate the use of thinner gauge metals, composites, and lighter weight plastics which contribute to lower energy consumption during vehicle operation.
Furthermore, the enhanced durability and longevity of EV battery packs bonded with battery adhesives reduce the need for frequent replacements, ultimately decreasing the demand for raw materials and minimizing waste generation. By promoting the use of advanced assembly practices and construction materials, structural adhesives play a crucial role in the development of a more efficient battery electric vehicle.
Conclusion
In conclusion, structural adhesives like Plexus MA7020 and DT2630LD have emerged as a vital component in the assembly and performance of electric vehicle batteries. By enhancing durability and safety, improving efficiency and performance, enabling weight reduction and design flexibility, and increasing efficiency, these battery adhesives contribute significantly to the advancement of electric vehicle battery packs. As the automotive industry continues to innovate and evolve, the role of structural adhesives in EV batteries will undoubtedly remain integral to the future of advanced transportation.
Adhesive technology is an important component of EV battery pack manufacturing. ITW Performance Polymers offers a full range of globally available adhesives to meet all critical battery requirements.
If you have questions about EV manufacturing with adhesives, technical questions about Plexus® acrylic adhesives, or bonding in general, contact Technical Support for more information.
Need some help? Ask a technical question and find a solution!
Further reading: Hybrid Adhesives: Greater than the Sum of its Parts?, Thixotropy, Viscosity and Rheology … Oh my!, What is fixture time anyway?, and Is it strong enough?.
For more stories like this, follow ITW Performance Polymers on LinkedIn and sign up for enewsletter in our website footer.