Post Takeaway
To best understand how Chockfast cures, or asked by many, how does it become hard, we discuss below key drivers and influencers to the chemical reaction and process including: The Chockfast resin (Part A), the hardener (Part B), mixing tools, environmental and recommended best practices to make them all work together. Read more on industrial epoxy hardening.
Outline
- Introduction
- How Chockfast Cures
- Mass Effect
- Working Time vs. Cure Time
- Initial vs. Final Cure
- Implications
Understanding the Chemical Reaction of Chockfast Epoxies: The Science of Heat
Ever wondered what makes Chockfast products so reliable for dynamic equipment installations? The secret lies in their chemistry. These industrial bonding solutions come in two main types: Grouts (which contain aggregates) and chocking products (which have special fillers mixed into the resin). Both start with two key ingredients: Epoxy resin and amine hardener.
But what happens when these components are mixed? Let’s dive into the cure cycle and understand the fundamental science behind the epoxy polymerization reaction.
The Magic of the Chockfast Curing Process: How Does It Get Hard?
When the epoxy resin and amine hardener are combined, a chemical reaction begins. The molecules from both materials essentially wake up and the rules of organic chemistry begin. The Epoxy resin woken up by the Hardener start linking up with each other, kind of like pieces of a puzzle coming together. Scientifically, the polymerization reaction is where the single resin molecule combines with the other unique components for its ultimate properties. This reaction process that creates heat is known as an exothermic reaction. How efficient and quickly the epoxy cure cycle happens depends on several factors:
- How well the foundation materials can absorb heat, also known as the Specific Heat Capacity of the materials
- The temperature of the surfaces it touches (like steel or concrete) as these can create a heat sink to cool or help maintain the reaction temperature
- The ambient temperature of the surrounding air
- How mass of much material you’re using in one spot as compared the same mass spread over a thinner or larger area
This exothermic reaction of heat generation isn’t just a side effect – it actually plays a crucial role in determining the Chockfast’s final properties of how strong and effective the final product will be. Getting it right is essential for ensuring quality and proper bonding with mounting surfaces.
The Mass Effect: Why Size Matters
One of the greatest takeaways to remember is how important the use of the reaction’s heat is to the product’s final properties. Of all the influences such as surface and ambient temperatures, the mass of the product will be one of the most important influences: By controlling the mass, or the more Chockfast material you pour in one spot, the more heat it generates. Below is a depiction on how different variations on a similar installation design affects the heat of reaction (exotherm) by the mass effect:
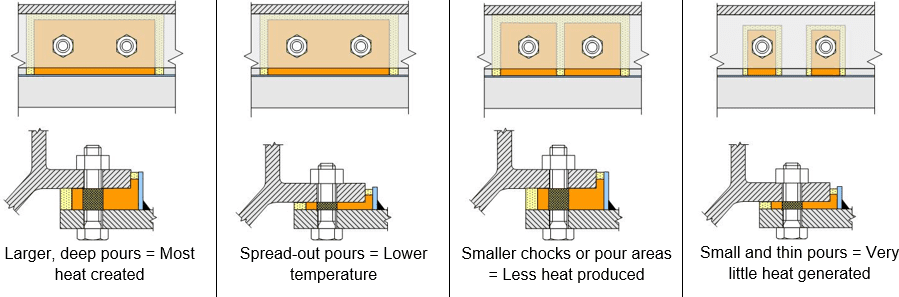
By controlling these variables, you ensure that the epoxy cures in a way that maintains its quality and performance. This “mass effect” is a key consideration in the chemical reaction of Chockfast Epoxies. The greater the mass, the greater the reaction temperature and the smaller or less concentration of the mass, the lower the temperature. However, it’s important to read the products technical literature that defines the upper and lower limits of the mass to assure the right range for a properly controlled outcome.
What Could Go Wrong?
If you pour too much at once or let things, get too hot, you might end up with cracks in your installation. To avoid this, consider:
- Breaking big pours into smaller sections
- Pouring in layers for large areas
- Adjusting the temperature of either the Chockfast or the work area
You pour too little and the final product may not reach its full potential. This may create early cracks during the installations or quickly under dynamic loads.
Implications for the Installer
While Chockfast epoxy grouts and chocks do not need additional heat to effectively cure, understanding the factors that affect the exothermic reaction of these materials is vital for proper installations.
Good installers know how to control a reaction’s heat and epoxy curing. By controlling the temperature of the installation area, the material, and the foundation components along with understanding how the mass effect affects the heat generated during the chemical reaction, large and small installations can be successful.
We will be looking more at how the chemical reaction affects Chockfast Installations in more detail in our upcoming posts on:
- Initial Cure vs Final Cure
- Temperature Effects on Chockfast
- Installations in Hot Weather
- Installations in Cold Weather
Final Thoughts
For the best results, go to our website (itwpp.com) and our Assets Library to find and refer to our technical datasheets/guides (TDS) of each product for application and curing temperature specifics, guidelines for mixing and pouring, and for learning more about epoxy grout chemical properties. If in doubt, contact Technical Services for additional advice on controlling the chemical reaction in epoxy grout or planning for the cure time for epoxy grout. Understanding the Chockfast epoxy strength development will ensure the highest quality installations and contribute to long-term equipment reliability.
To further discuss the Chockfast curing process of your specific application or to discuss any of our machinery maintenance adhesives, please contact ITW Performance Polymers’ Technical Services or your local Chockfast Worldwide Distributor Network representative.
View all our Technical Data Sheets and Safety Data Sheets. Need some help? Ask a technical question and find a solution!
Further reading: Cheat Sheet: Chockfast® Epoxy Grout Typical Installation Steps and Critical Machinery Installation In Cold Weather? Find Out How To Plan For Success.
For more stories like this, follow ITW Performance Polymers on LinkedIn and sign up for enewsletter in our website footer.