Post Takeaway: Learning how everything works together. Understanding the components of Dynamic Equipment Foundation Systems
Introduction
Unplanned downtime in manufacturing can be incredibly costly, reaching up to $260,000 per hour according to a study by Aberdeen Research. The “True Cost of Downtime 2024” report from Siemens also shows that downtime in heavy industries now costs four times more than it did five years ago. These eye-opening numbers highlight just how crucial it is to prevent unplanned downtime and follow best practices to extend the Mean Time Between Failure (MTBF).
Dynamic equipment foundations are specialized systems designed to support heavy machinery, boost operational efficiency, and prevent costly unplanned downtime. However, designing and installing these foundations can be quite challenging due to the complex interplay of various components. A poorly designed foundation or improper installation can lead to chronic issues like high vibration, rotating assembly “rubs,” poor seal life, mechanical failures, and even hazardous work environments.
To be effective, a foundation design for machinery must be viewed as a system, not just a collection of parts. We call this a Monolithic Foundation System, because it needs to act as a unified, unbroken structure. This blog provides an overview of the components that typically make up a dynamic equipment foundation system and share best practices for industrial foundation engineering to aid construction installers, engineers, and equipment designers.
Key Components of a Dynamic Equipment Foundation System
As foundation system designs can vary widely, in this paper, we focus on best practice recommendations for designing and installing soil-supported foundation systems for dynamic equipment. The typical components of such a system include the Subsurface/Soil, a Concrete Foundation Block, Anchor Bolts, Epoxy Grout, and the Machine Mounting Surface, as shown in Figure 1.
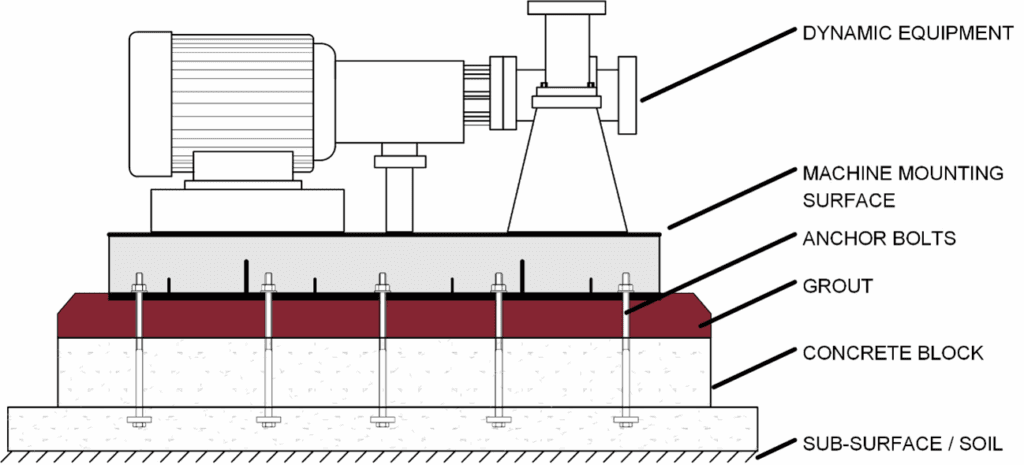
Subsurface/Soil
Proper soil investigation and assessment of bearing capacity are essential to ensure the foundation’s stability and reduce the potential for settlement over time. The subsurface must be designed to support the dynamic load analysis without exceeding the soil’s allowable bearing capacity or settlement limits. This is crucial to prevent damage to piping system connections, internal machinery alignment, or other auxiliary equipment.
Concrete Block
The concrete block, usually made of reinforced concrete, should provide adequate strength and rigidity. Key design considerations include mass, stiffness, and geometry, which influence the foundation’s ability to support dynamic loads effectively and absorb damaging vibrations.
Anchor Bolts
Anchor bolts are used to secure machinery to the foundation. Proper placement and design of anchor bolts are crucial for maintaining the proper anchor load on the equipment. Additionally, protecting anchors from corrosion is essential to ensure long-term stability and performance.
Grout
Grout is used to preserve the precise machine alignment and mitigate operating loads, as well as to protect the foundation system. Both cementitious non-shrink grouts and epoxy grouting solutions are commonly used.
Epoxy grouts like Chockfast Red and Chockfast Orange offer advantages for dynamic loads, including chemical resistance and resilience. Comparing the three main materials used in foundation construction—steel, concrete, and epoxy—it is also important to understand how these substrates perform in terms of vibration absorption. Epoxy grout installations, due to their low modulus of elasticity, provide nearly 30 times the vibration absorption capacity of steel and 6 to 10 times better than cement-based materials.
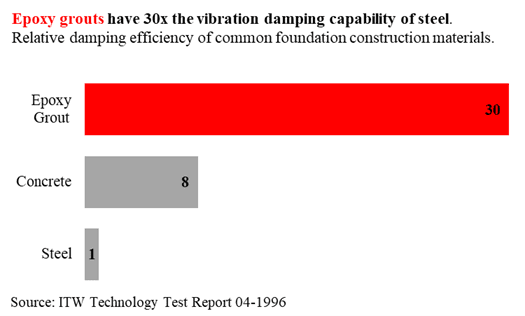
Machine Mounting Surface
Machine Mounting Solutions involve structural mounting surfaces such as base plates, sole plates, and mounting rails, which are critical for securing machinery to the foundation. Ensuring accurate leveling and alignment is vital for optimal machine performance and longevity.
Conclusion
Dynamic foundation systems are integral to the efficient operation of heavy machinery. By understanding and implementing best practices for the key components—subsurface/soil, concrete block, anchor bolts, machine mounting surfaces, and grouting—engineers, designers, and installers can significantly extend the MTBF (mean time between failure), optimize planned downtime, and prevent the costly unplanned downtime. Collaboration between all stakeholders is essential to achieve design and installation best practices, as was presented at the 2020 European Forum on Reciprocating Compressors (EFRC) and the 2023 Turbomachinery and Pump Symposium.
For more information on heavy equipment foundations including Chockfast epoxy grouts and chocks, please contact ITW Performance Polymers Technical Services or your local Chockfast Worldwide Distributor Network representative.
View all our Technical Data Sheets and Safety Data Sheets. Need some help? Ask a technical question and find a solution!
Further reading: Cheat Sheet: Chockfast® Epoxy Grout Typical Installation Steps and Critical Machinery Installation In Cold Weather? Find Out How To Plan For Success.
For more stories like this, follow ITW Performance Polymers on LinkedIn and sign up for enewsletter in our website footer.