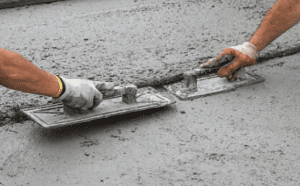
Introduction to Concrete Repair and Concrete Sealing
Concrete and other masonry products are long-lasting, energy-efficient and versatile building materials. Many of our historic buildings are made of concrete or masonry. With new additives and other technical enhancements, Modern concrete is even more of a durable building material. When concrete is properly selected for an application and mixed, poured on site and applied with a high-quality sealer, it also will have a very long lifespan and is usually maintenance free, but it will still need maintenance and protection. This is equally or more important for older structures built using older concrete chemistries and that remain in use and where we need to keep their functionality through countless environmental conditions. In such situations, it is important to regularly evaluate the concrete to ensure it has received the care it needs to remain useful.
The integrity of concrete can be increased by using cement or other types of coatings and crack fillers. High-performance epoxy coatings are used with conventional indoor and exterior structures, as well as for marine applications, to protect steel and concrete from mechanical and chemical damage. Epoxy coating solutions consist of two or more ingredients that, when mixed and applied as a coating, chemically react to form a protective layer with exceptional adhesion, corrosion and erosion, and impact resistance.
Basic Steps
The lifespan of today’s concrete can be extended by creating and following a well-planned maintenance program. Implementing an effective maintenance program to extend the life of a concrete structure is often much more economical than not doing so. Failure to ensure proper maintenance is performed promptly will typically result in costly repairs or replacements. Repairing and protecting concrete as part of a routine maintenance system consists of the following well known and common seven basic steps:
1. Determine the possible causes of damage:
The first and very important step in protecting or repairing damaged or damaged concrete is to correctly determine the type of and what caused the damage. Knowing what caused the damage and reducing or eliminating that cause will extend the life of your concrete repair.
2. Assess the extent of damage:
Determine how badly the concrete is damaged and how this damage affects the serviceability of the structure (how long, how wide, how deep, and what part of the structure is affected). It is also possible to predict how quickly the damage will increase and how it will develop.
3. Assess repair needs:
Degree of repair needed. Not all damaged concrete needs to be repaired immediately. There are many factors to consider before deciding on repairs. Of course, repair is necessary if the damage affects the safety or safe operation of the structure. Likewise, concrete replacement should be carried out when deterioration has reached a point or is progressing so quickly that the future usability of the structure is impaired.
4. Selecting a Repair Method and Material:
Once you have completed the first three steps of the concrete repair process, it is usually easier to select the appropriate repair methods and materials. These steps determine the type of conditions the concrete repair must withstand, the time you need to complete the repairs, and the time frame needed. These steps should be considered in addition to the required application.
For example, if a concrete repair is required, the repaired concrete surface must be able to withstand the elements that caused the original damage, or at least be able to effectively resist the elements and accept a well-penetrating seal to ensure complete protection. Penetrating sealants, including silanes, siloxanes and epoxies, provide a cost-effective way to add more protection to new and existing surfaces.
When used correctly, crack sealants can provide protection from salts and moisture while increasing resistance to destructive corrosion of reinforcements and damage from freeze thaw cycles. Concrete crack sealers can be used alone or in combination with a concrete crack repair solution. Sealants can be applied during original construction, as part of a maintenance program, and for protection or repair purposes. The choice of the most appropriate protective treatment largely depends on the correct assessment of the exposure conditions.
For example, concrete sealers, coatings, and concrete repair compounds that provide good protection from the elements in a substantially dry environment may perform poorly in wet conditions, such as: B. on some bridge curbs and railings, calming pool walls and pillars. It is also important to consider the mechanical properties of the sealant to ensure it is suitable for the application, e.g. B. for sealing a concrete expansion joint.
5. Preparing existing concrete for repair:
Preparing existing concrete for repair is very important to ensure its durability. It is just as important as renewing the concrete surface. In this preparation phase, all damaged and deteriorated concrete is removed to create a solid surface to which the repair material can adhere well. If this step is not performed correctly, the repair will likely end prematurely, regardless of the quality of the other steps. It is important to remove damaged or weak concrete before applying repair material.
6. Apply repair method:
Concrete sealants and coatings are applied to dry, cured concrete as a maintenance and repair procedure to reduce or prevent the ingress of water, aggressive solutions or gaseous media. They help reduce or prevent associated damage such as reinforcing steel corrosion, freeze-thaw cycles, carbonation or sulfate damage. In particularly harsh environments, a sealant can be coated with an epoxy solution because various types of epoxy resins are specifically formulated to have very low viscosity to penetrate hairline cracks in concrete and resist chemical attack.
They can be easily spread on horizontal concrete surfaces with a broom or squeegee. They can penetrate the concrete surface to a depth of approximately 1/16 inch or less, but are most effective when penetrating and sealing cracks in the surface, and also act as a membrane-forming system when two or more applications are made.
7. Carry out repairs properly:
All common repair materials must be properly cured. Curing is typically the final step in the repair process, followed by cleaning and demobilization. Often the curing step is shortened, performed haphazardly, or skipped entirely because workers want to leave the site quickly. Proper curing is critical to the long-term performance of the repair material. The money and effort invested in properly curing the repair is a good investment to ensure long-lasting performance.
Improper or insufficient curing can result in significant deterioration in the performance of the repair material and ultimately loss of money. In the best case, inadequate curing will shorten the life of the repairs, but inadequate or inadequate curing will result in the repairs having to be removed and replaced.
Devcon Concrete Repair Solutions
Devcon offers a complete range of chemical construction repair products and proven technologies using epoxy and PU chemistry. Here are our recommendations for concrete resurfacing, repair, and protection:
- Devcon® Deep Pour Grout™: Filled epoxy for rebuilding worn concrete or pouring equipment pads up to 6 deep.
- Devcon® Epoxy Coat™ 7000 AR: 100% solids floor coating system to protect surfaces from severe acid and chemical attack.
- Devcon® Epoxy Coat™ 7000 (Non VOC): 100% solids, self-leveling floor coating system that can be applied to smooth or mildly spalled concrete.
- Devcon® Epoxy Concrete Sealer: 100% solids epoxy that provides a durable, chemical-resistant coating.
- Devcon® Floor Grip: Heavy-duty epoxy compound with silicone carbide granules, for an exceptional non-skid surface.
- Devcon® Floor Patch™: All-purpose concrete patching compound with a compression strength of 8000 psi.
- Devcon® Floor Patch™ (Fast Cure): Fast-curing concrete patching compound with a compression strength of 8000 psi.
- Devcon® Floor Patch™ Resurfacer: Self-leveling, filled epoxy system for repairing heavily spalled concrete floors.
- Devcon® Ultra Quartz™: Heavy-duty, premium floor patching system with excellent chemical resistance.
Conclusion
ITW Performance Polymers provides the experience of over 70 years in research and manufacture of specialty Devcon epoxy and urethane products for concrete protection and renewal. Devcon was founded in 1950 and the first product formulations pioneered the development of epoxy based adhesives and coatings for use with concrete. Since then, Devcon products have continued to break new ground in epoxy technology development for architects, engineers, consultants, specifiers, users, and contractors worldwide.
View all our Technical Data Sheets and Safety Data Sheets. Need some help? Ask a technical question and find a solution!
Further reading: Durability With Devcon® Protective Coatings: Proven In Multiple Industries and The Top Four Types Of Wear Impacting Industrial Equipment.
For more stories like this, follow ITW Performance Polymers on LinkedIn and sign up for enewsletter in our website footer.