Installation of all 70 wind turbines in the Wikinger Offshore Windfarm has been completed and ITW Performance Polymers is proud to have delivered the challenging grouting solution for the project.
The Wikinger windfarm site is located off the German coast in the Baltic Sea and will cover an area of 34 km2. It will be comprised by 70 wind turbines, each generating 5 megawatts. The water depths of the site demand fixed four-legged jacket solutions, making Wikinger one of the largest jacket foundation windfarms in the world.
In total, the windfarm will produce up to 350 megawatts and reduce CO2 emissions by up to 600,000 ton each year.
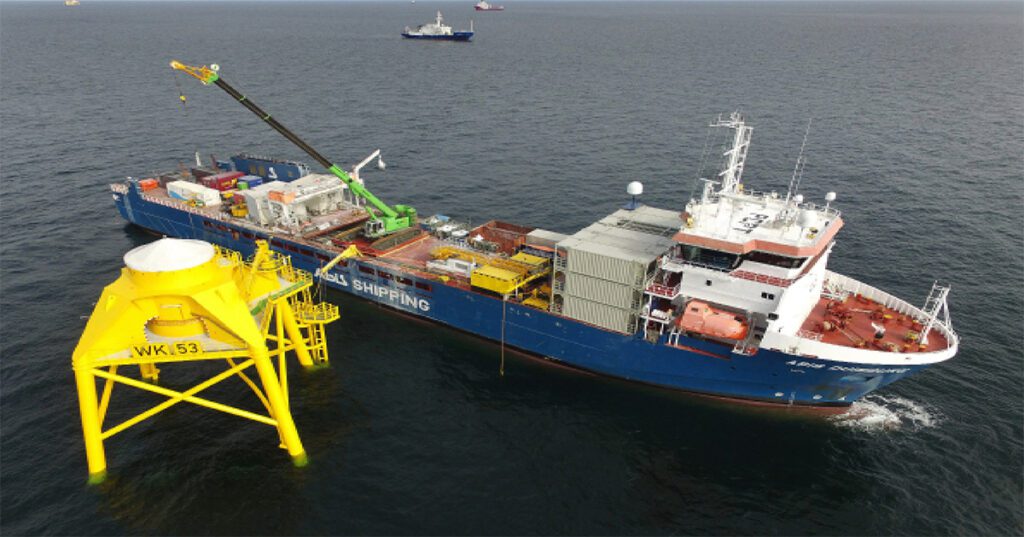
GROUTING IN DIFFICULT ENVIRONMENTS
Between July 26, 2016 and January 9, 2017, ITW Performance Polymers was working with Offshore Wind Force on grouting the 70 jacket installations for the Wikinger project. Approximately 10,500 ton of Ducorit® S2 material was mixed and pumped to make the 280 grouted connections. Working within a narrow timeframe, we were compelled to maintain a high pumping rate in order to successfully complete the grouting. Through the use of our double spread equipment and double shifts, we managed an average pumping rate of around 40 ton per hour. The high pumping volume helped to ensure a smooth installation process all around and we are proud to say that the installations were an immense success.
SPECIALIZED MOCK UP TESTING
Due to water depths of 37-43 meters, the installations required cutting edge technology. There- fore, we performed a scale mock up test of our Ducorit® S2 prior to the project to prove that our product would be the right material for the job. The mock up was done in our testing facilities in Aalborg, Denmark and was witnessed and approved by German ZiE grout experts.
The key purpose of the test was to investigate the grout behavior in a scenario with a 700mm drop in water, as this was a design requirement for the installations. A drop such as this could result in a high level of spread and segregation in the grout. However, the test proved that Ducorit® S2 is capable of withstanding this challenge. Furthermore, the test proved Ducorit® S2’s minimal need for overflow and its ability to perfectly enclose sheare keys in the foundation structure, making it the ideal material for this type of jacket installation.
ONE STOP SHOP
During the Wikinger project we proved our ability to provide turnkey solutions once again. ITW Performance Polymers handled all logistics and managed delivery directly to the quay side. Normally we deliver our big bags by trucks, but for the Wikinger project we succeeded with using trains as our primary means of transport. This is a more cost-efficient solution and represents future opportunities for both our clients and us.
The whole grouting process was led by our own offshore supervisors ensuring correct installation of our product. The extensive experience of our offshore supervisors combined with our 2-ton big bag solution also enabled us to conduct the installation directly from a floating vessel instead of a more time-consuming jack up solution. Installing directly from a DP2 vessel further in- creased installation flexibility and eased planning procedures by enabling efficient utilization of narrow weather windows. This optimized process allowed us to install up to four jacket structures within 48 hours.
For more information, please contact:
Flemming Frost Hansen
Business Manager, Offshore Wind and Oil & Gas Mail: ffhansen@itwpp.com
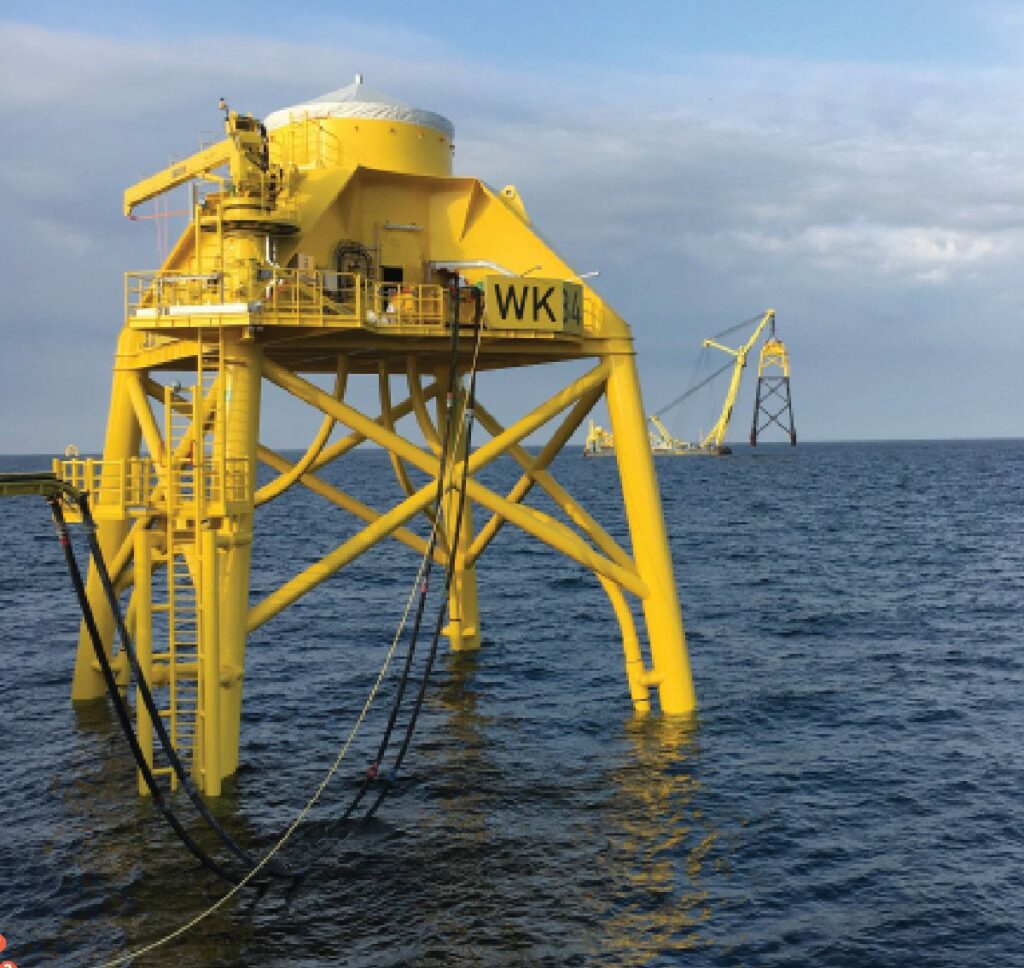
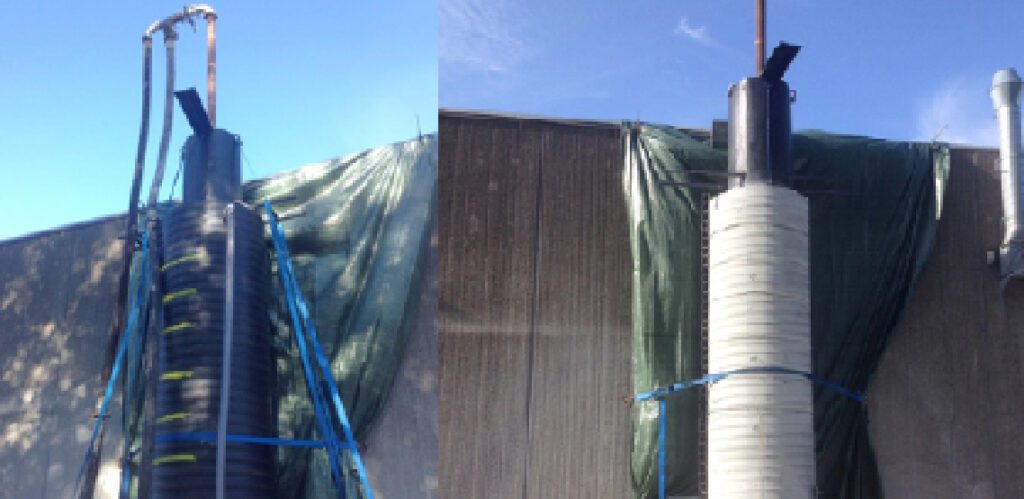

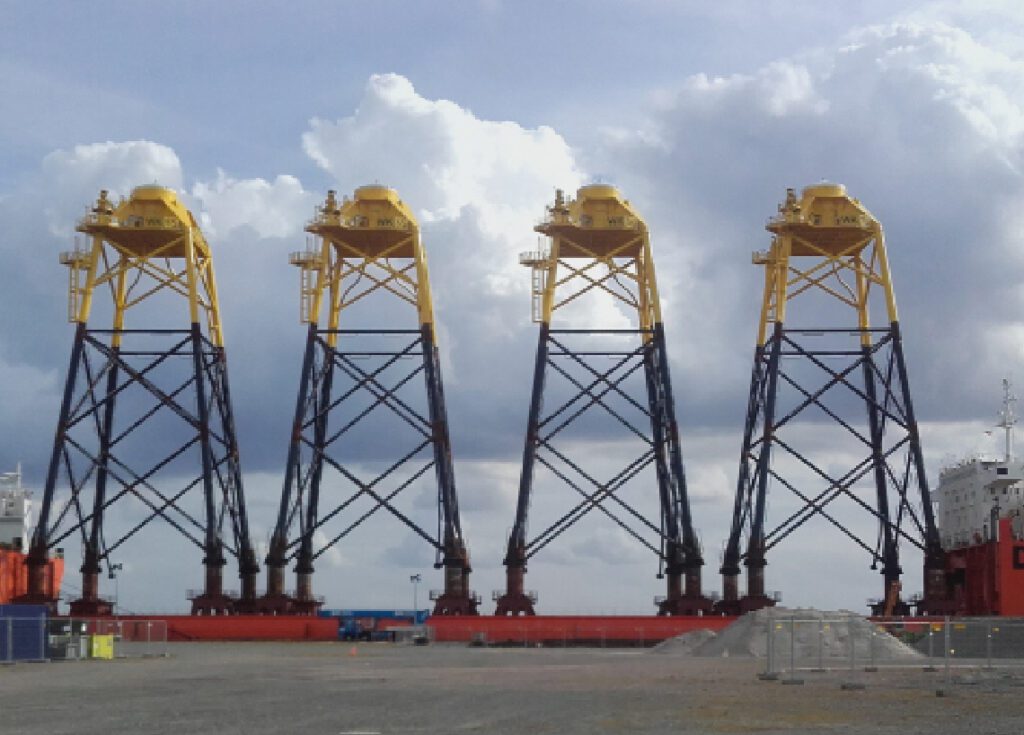
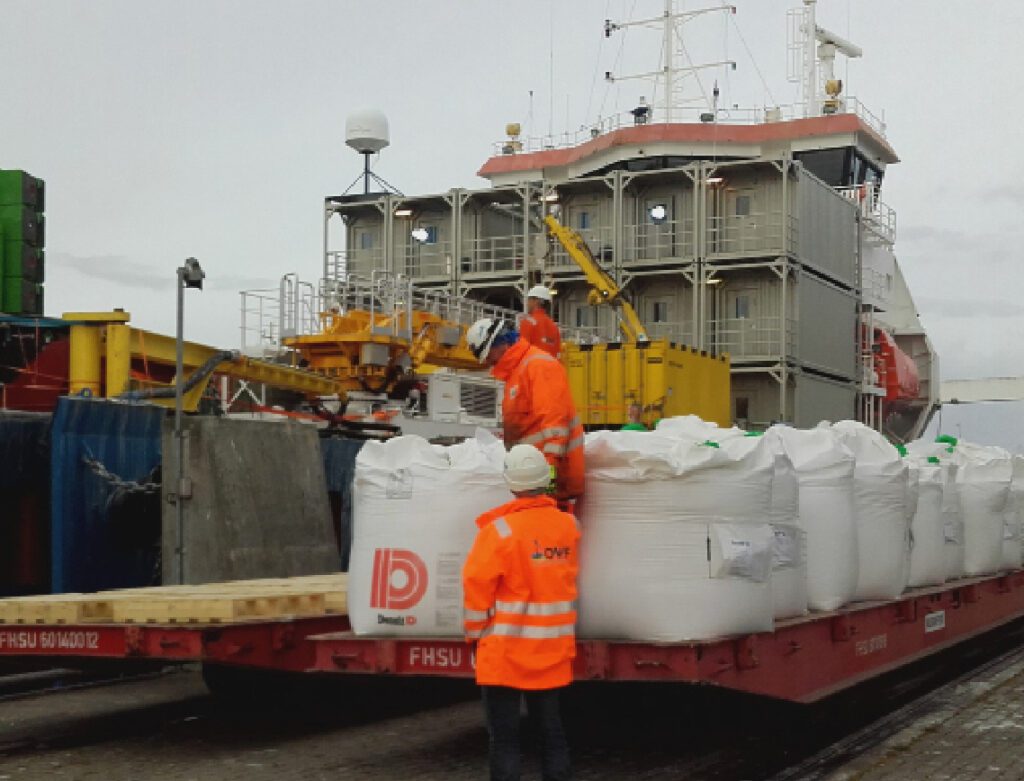