ITW Performance Polymers and Pro-Op Industries successfully relieved IDM Meyerton of shell replacement issues by installing a UHCP abrasion lining that ensures long-term stability.
The client, IDM Meyerton, had a challenge with a rotary dryer used for slag drying. The severe wear and abrasion caused by the slag wore through the inside of the dryer, causing the need for replacement of the dryer shell.
The costs related to replacing dryer shells inspired IDM Meyerton to look for an alternative abrasion solution. The combination of temperature fluctuations inside the dryer and the heavy abrasion and corrosion from the wet slag were the main challenges for solving the issue.
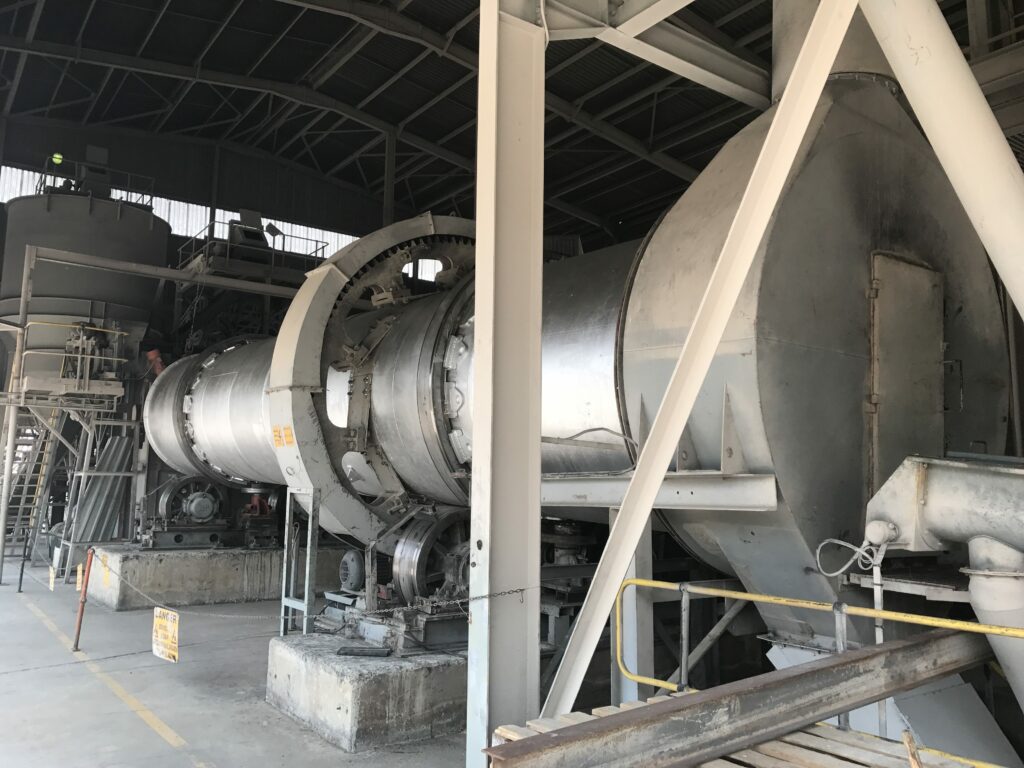
The client had tried a large variety of other solutions for this combination, including high temperature epoxy and high quality steel. But with all prior solutions, the dryer
broke after less than a year.
ITW Performance Polymers and Pro Op Industries proposed a UHCP abrasion lining made from Densit® WearFlex 2000 HT to eliminate the need for shell replacements and thereby significantly reduce long-term costs.
ITW Performance Polymers has more than 30 years of experience with wear and abrasion linings and ensure products and solutions of the highest possible standards.
Anchoring System – The Baseline for Quality
To ensure proper lining installation and optimal product performance, a stainless steel anchoring system was carefully installed inside the dryer. A properly installed anchoring system is one of the keys to the installation process. Thus, the ITW Performance Polymers supervisor continuously checked and approved the quality of the anchoring system during the installation process.
Lining Installation
After the installation of the anchoring mesh, the installation of the actual abrasion lining was commenced. Our technical experts determined that a 30mm abrasion lining was needed to maximize the life expectancy of the installation.
Installation was done in two rounds. First, the bottom half of the dryer was lined. Second, the dryer was turned and the other half of the dryer was lined. This enabled the installers to never perform any overhead installations, which would slow down the process and increase the risk of variations in installation quality.
After successfully installing the lining, the team allowed the Densit® lining enough hardening time to gain 60% of the final product strength before putting the dryer back into service.
Result
The slag dryer is once again fully operational. Furthermore, the long life expectancy of the Densit® lining means that the need for shutdowns and maintenance will be significantly reduced in the future. Where previous solutions lasted no longer than 1 year, the life expectancy of the Densit® lining is 4-8 years under normal operation conditions.
ITW Performance Polymers would like to thank Pro-Op Industries for the good cooperation and successful lining installation process.
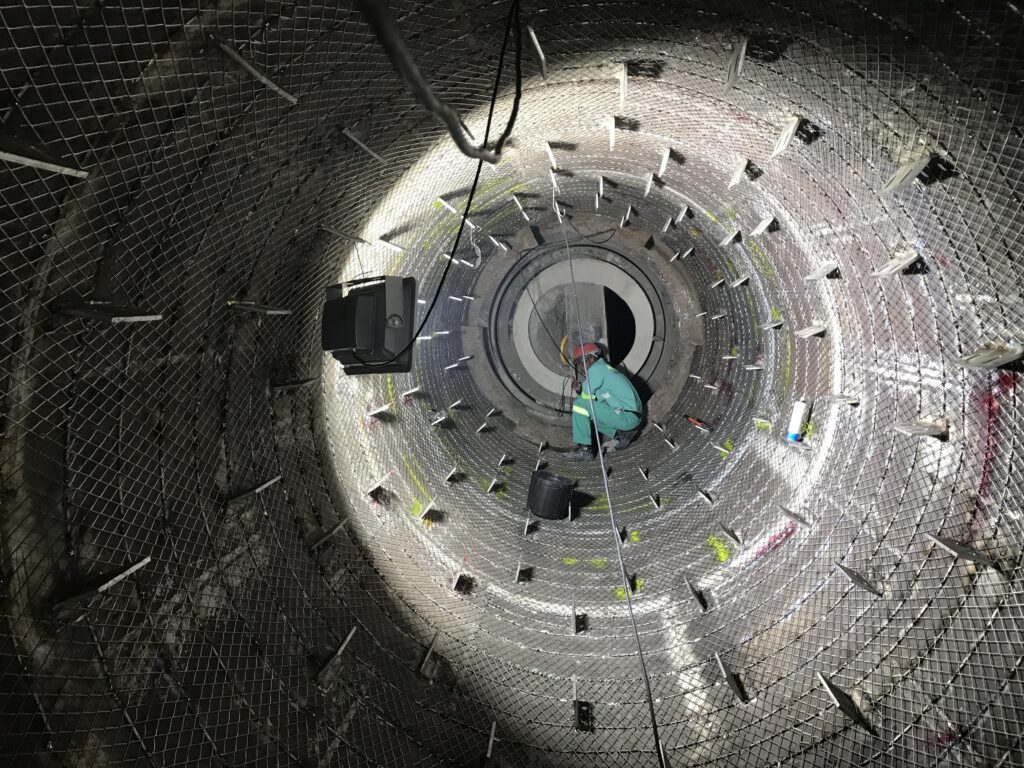

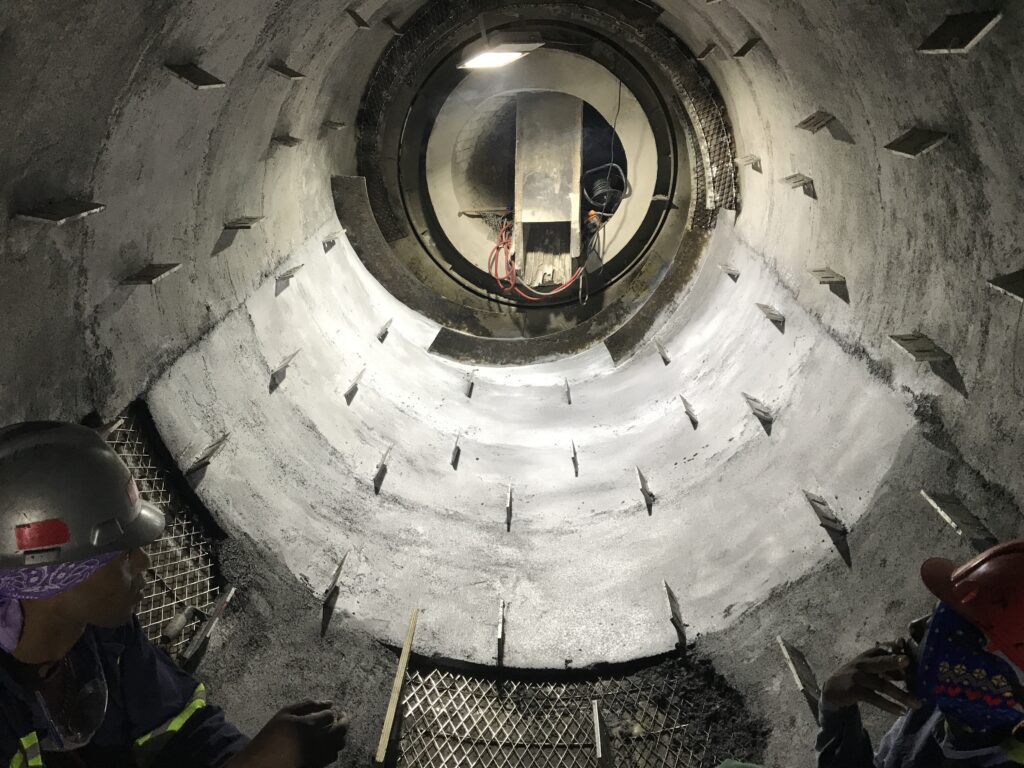
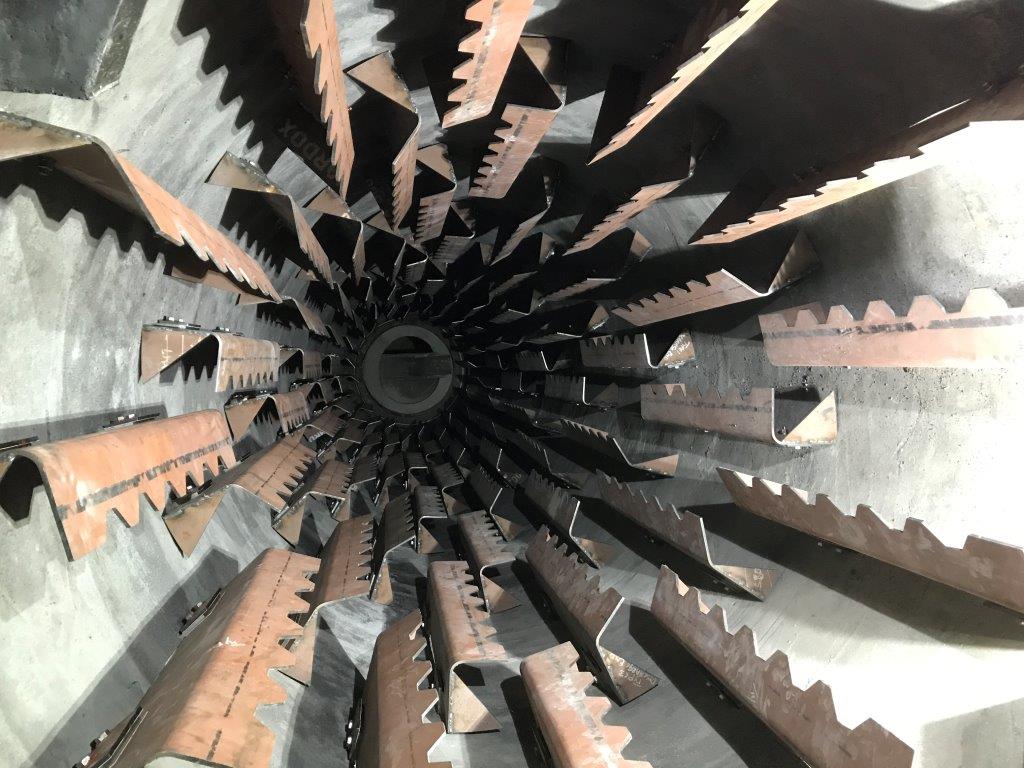