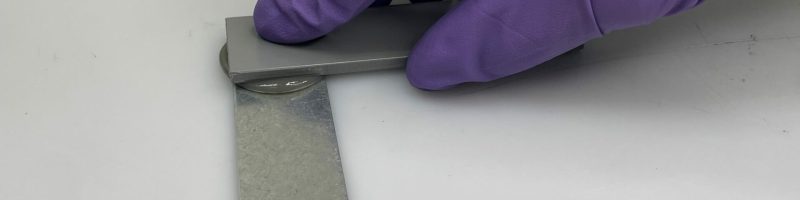
Introduction
Finding the right glue for metal to metal bonding can be difficult. Even knowing where to start can be an overwhelming task! There are many factors to consider when selecting the right metal adhesive including:
- Type(s) of metal being bonded
- Surface quality of the metal
- Environmental resistance
- Appropriate speed for your process
- Static or dynamic stresses on the assembly
One adhesive that satisfies all design criteria can be like trying to find that “unicorn” solution. But why complicate things? Plexus offers a full portfolio of acrylic adhesives specifically designed to form the strongest, most reliable metal bonds in the toughest of scenarios.
The Right Metal Adhesive for the Right Type of Metal
Gluing metal to metal might sound simple, but how does the type of metal influence your options? Many adhesives will perform well only with specific metals or in specific conditions. Many metal to metal glues are only capable of reliably bonding one type of metal to itself. Fortunately, Plexus is not limited in this way.
Plexus acrylic adhesives were designed to overcome the challenges presented by traditional joining methods. Where mechanical fasteners (rivets, screws, pins, etc.) create dangerous stress concentrations, Plexus adhesives distribute structural loads evenly and make metal joints safer. If a stainless steel part needs to be joined to an aluminum part, an acrylic adhesive (such as those found under our Plexus brand) is an excellent choice. Bonding dissimilar metals poses no issue to our adhesive technology because Plexus was built around the need for a nearly universal bonding solution. This includes hard-to-bond metals like electrogalvanized (EG) steel, hot dipped galvanized (HDG) steel, anodized aluminum, and high polish metals.
Many metal bonding applications also include the need to bond components made of other materials. Bonding in composites (FRP, GRP, carbon fiber, etc.), plastics (ABS, polycarbonate, nylon, etc.), and coated metals (E-coat, powder coat, paint, etc.) poses no challenge to Plexus metal adhesives. Where many other adhesives fail to “do it all”, Plexus will permanently bond to the toughest materials.
Different Metals, Different Surfaces
The surface quality of a metal part is a major factor for how many metal adhesives will perform. Most adhesives are not designed to adhere to dirty, dusty, or oily metal surfaces. Other adhesives often require surface preparation like:
- Heavy abrasion (sanding or grit/shot blasting)
- Flammable solvents for cleaning
- Plasma treatment
- Chemical primers
Plexus metal bonding adhesives are not restricted by any of these. Designed to bond to the toughest and dirtiest of surfaces, our acrylic adhesives require no or minimal surface preparation. Tested and used in environments with dust, grime, gravel, dirt, and surface oil concentrations over 9 g/m^2, Plexus acrylic glue forms structural metal bonds that are second to none.
While acrylic adhesives are known to bond to the toughest surfaces, there is always room for unique situations. Regardless of the adhesive solution chosen, it should always be tested with your material to ensure it will meet your needs. Check with our Technical Services department if you have the right adhesive for your material and application.
Designed for the Real World
When selecting a glue for metal to metal bonding it is also important to take into consideration where it will be used and what kinds of environments it will need to survive. Plexus acrylic adhesives are used as solutions to a wide range of problems:
- Surviving high vibration environments
- Freeze/thaw and thermal shock resistance
- Galvanic corrosion resistance
- Strength retention over a wide range of usage temperatures
- Reducing stress concentrations
With our patented core shell technology, Plexus acrylic adhesives are often seen as one of the toughest metal bonding solutions. This toughness lends itself to mitigating the risks associated with coefficient of thermal expansion (CTE) differences. Where rivets and screws are known for creating stress concentrations and corrosion, Plexus acrylic glue distributes stresses evenly throughout the bond area. As a result, our metal adhesives provide long lasting fatigue resistance in dynamic applications. Since they are not electrically conductive, they can also eliminate the influence of galvanic corrosion by isolating metal to metal joints while forming fully structural bonds. Plexus retains structural strength for any application in the most extreme of real world conditions.
Conclusion
When choosing an adhesive for your metal bonding application, Plexus acrylic adhesives are the first and last glues you will need. Designed to adhere to most metals with either no or minimal surface preparation, we believe Plexus metal bonding adhesives will exceed your expectations. We eliminate the pain points of mechanical fasteners and welding while surpassing the shortcomings of other structural metal to metal glue. Where other metal bonding adhesives fail, Plexus thrives.
For more information on our Plexus adhesives, view our brochures and value sheets in our Assets Library. To find more formation on which Plexus metal bonding adhesive is best suited for your application, you can view all our Technical Data Sheets and Safety Data Sheets.
Need some help? Ask a technical question and find a solution!
Further reading: Thixotropy, Viscosity and Rheology … Oh my!, What is fixture time anyway?, and Is it strong enough?.
For more information like this, follow ITW Performance Polymers on LinkedIn and sign up for enewsletter in our website footer.
ITW Performance Polymers is an international leader in structural adhesives, grouting and chocking compounds, and wear-resistant coatings and repair products. Contact us to learn more about these products and their applications.