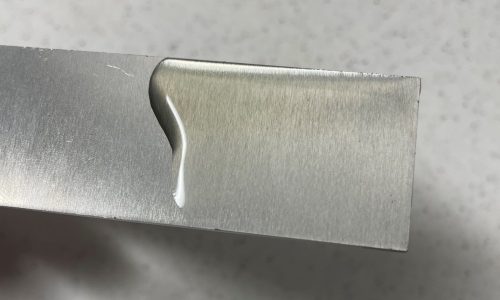
When it comes to automotive manufacturing, ensuring strong bonding to oil contaminated metal (oily metal adhesion) has always been a challenge. With the push for lighter, stronger vehicles, manufacturers are turning to high-performance adhesives to bond oily surfaces applications effectively. One standout in this field is Plexus MA8000 Series, a powerful adhesive family with varying working times, designed to work even on metal surfaces contaminated with oil.
The Challenge with Bonding Oily Surfaces & Oily Metal
During production, metal parts are often coated in lubricants to prevent corrosion, oxidation, and aid machining or stamping. While helpful in the process, these oils often make it difficult for adhesives to form strong bonds later in the assembly process. Traditional methods like welding and mechanical fasteners aren’t always practical due to part configuration, or even cosmetic concerns, especially with lightweight vehicle materials such as aluminum and high-strength steel that require more delicate joining or bonding techniques. In many cases there is also the need for joining dissimilar metals, which is where structural adhesives play an important role.
A Game-Changer in Structural Bonding for Automotive Parts
Thanks to advancements in metal bonding, structural adhesives like Plexus MA8000 Series now provide a reliable solution. This adhesive family creates strong, long-lasting bonds on oily surfaces without requiring extensive prep work. That means faster production, reduced costs, and improved automotive structural integrity.
Why High-Performance Adhesives Matter
- Increased Durability & Crash Protection
Modern automotive adhesives and particularly crash-resistant adhesives help absorb dynamic energy, reducing stress points and enhancing safety. Unlike rivets and welds, adhesives distribute force more evenly, minimizing the risk of failure under extreme conditions.
- Effective Bonding on Contaminated Surfaces
With Plexus MA8000 Series, manufacturers don’t need to spend extra time cleaning every metal surface. These adhesives are capable of bonding directly to oily metal surfaces, making production faster and more efficient while still meeting high performance standards.
- Lighter Vehicles, Better Efficiency
By reducing the number or eliminating traditional fasteners with the use of structural bonding adhesives for automotive and large transportation parts, manufacturers can enhance quality and reduce weight without sacrificing strength. Each potentially contributing to Lighter cars, enhanced fuel efficiency and ultimately lower emissions; A win for both performance and sustainability.
Acrylic Adhesives vs. Traditional Epoxies
While traditional epoxy adhesives have shown themselves as a proven technology in many metal bonding applications, structural acrylic adhesives also have a proven history. So, how do epoxies and acrylic adhesives compare when it comes to bonding oily metals? Considering our own Devcon epoxies, such as Devcon HP250, are proven reliable structural joining solutions for metals, it’s important to look at surface preparation. However, when an oily metal surface is not cleaned it often will underperform from its expected ultimate performance.
While epoxies continue to excel in numerous metal bonding applications, they aren’t the most reliable when it comes to bonding oily surfaces. Newer technologies such as our acrylic metal bonders like the Plexus MA8000 Series, were specifically formulated with automotive manufactures and focusing on oily metal adhesion. Plexus MA8000 Series and other Plexus metal bonders provide a simplified approach from start to finish, helping OEMs and Teir suppliers meet high production demands.
The Future of Automotive Adhesion
As automotive manufacturers focus on making vehicles lighter, stronger, durable and more sustainable, high-performance adhesives will continue to increase their role in this market. Bonding solutions like Plexus MA8000 Series are changing the way manufacturers approach bonding from intentionally modified surfaces to minimally prepared such as bonding oily surfaces, ensuring cars are built to last.
By embracing new automotive adhesives, manufacturers can improve safety, efficiency, and durability while keeping up with production demands. The future of car manufacturing is evolving, and the increased design freedom from structural bonding solutions are helping to lead the way.
For more information on our Plexus adhesives, take a look at our selector charts. Contact our Technical Services Department for more information on which Plexus adhesive is best suited for your application.
View all our Technical Data Sheets and Safety Data Sheets.
Further reading: Thixotropy, Viscosity and Rheology … Oh my!, What is fixture time anyway?, and Is it strong enough?.
For more stories like this, follow ITW Performance Polymers on LinkedIn and sign up for enewsletter in our website footer.
ITW Performance Polymers is an international leader in structural adhesives, grouting and chocking compounds, and wear-resistant coatings and repair products. Contact us to learn more about these products and their applications.