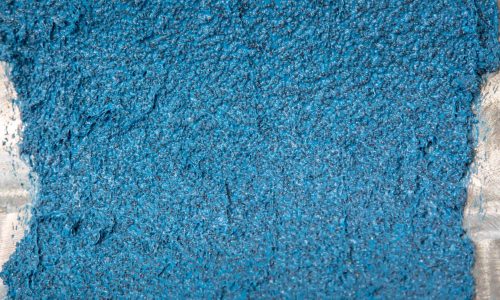
Introduction
If you’ve spent some time exploring our website, you’ve seen how Devcon coatings protect equipment from the extreme abrasion of rock and base ore materials in the mining industry. Coatings and the surfaces they protect can also face severe attack by harsh processing chemicals and fine particles, not just rocks and gravel visible to the eye. Sometimes, a coating must protect against both macroscopic and microscopic threats at the same time, such as on a tank or pump handling an abrasive liquid slurry that is also corrosive or caustic. If your tanks, pumps, valves, machinery, or floors are exposed to strong acids or corrosive substances, Devcon’s high chemical resistance coatings can save you money by extending both the time between repair or recoating and the lifetime of the equipment itself.
Advantages of Devcon Technology
One of the most important factors behind a chemical resistant coating is the crosslink density, or the number of connections between its polymer chains to create a 3-dimensional network. Inexpensive plastics such as polyethylene consist of non-crosslinked polymer chains and can be easily deformed, broken, dissolved, or melted. Devcon’s industrial strength coatings are formulated with proprietary epoxy chemistries (often two part epoxy) and curing agents to achieve the ideal balanced degree of crosslink density. The resulting interconnected network prevents water or liquid chemicals from reaching the substrate. Low-cost paints with little or no crosslinking will allow water or chemicals to penetrate to the surface below. Metal under the paint film will corrode and the coating itself will blister and peel off.
Additionally, Devcon’s industrial coatings contain proprietary coupling agents which chemically help to adhere the binder polymer to the intentionally added solid mineral particles present in the cured product. As an example, some of our coatings contain ceramic beads to achieve outstanding abrasion resistance and these beads are chemically coupled to the polymer network to prevent moisture or chemicals from penetrating the film.
Sulfuric Acid Resistance
Sulfuric acid is commonly used in oil refining processes. Equipment handling sulfuric acid is enclosed by secondary containment, which consists of concrete floors and berms to contain spills. In many cases, secondary containment areas are coated with an ordinary industrial floor coating. If the secondary containment area only experiences acid exposure in a rare emergency such as a tank bursting, this might be an acceptable solution. However, many secondary containment areas are exposed to frequent small spills and leaks, and a conventional floor coating will require frequent replacement under these conditions.
Devcon Epoxy Coat 7000 AR (AR stands for acid resistance) can withstand 98% sulfuric acid, a feat very few coatings are capable of performing. This formulation is based on an epoxy novolac resin system, known to provide a very high degree of crosslinking for outstanding chemical resistance also useful for concrete resurface or repair.
Abrasion and Chemical Resistance in One Coating
Devcon Brushable Ceramic, Devcon EZ-Spray Ceramic, and Devcon Wear Guard 300RTC (RTC stands for room temperature cure) are among some of our top recommended chemical resistant coatings when a substrate must be protected from wet chemical and abrasive attack simultaneously. Ore processing equipment in mines must be protected from abrasive slurries containing strong acids that corrode metal.
Devcon Brushable Ceramic has a track record of success in protecting pumps, valves, pipes, and tanks from simultaneous chemical and abrasive attack in mining applications, protecting expensive assets and prolonging the intervals between costly equipment shutdowns.
Devcon EZ-Spray Ceramic offers the same benefits in a convenient sprayable cartridge form, saving time and labor to get your equipment back into service faster and at lower cost.
Devcon Wear Guard 300RTC contains ceramic wear-resistant beads in our unique resin binder system for maximum resistance to abrasion and chemical attack in extreme environments, such as for screw conveyors and tanks in contact with abrasive, acidic ore slurries at high temperatures.
Conclusion
- Devcon’s proprietary chemistries give outstanding chemical resistance.
- Devcon Epoxy Coat 7000 AR withstands concentrated sulfuric acid in petrochemical refineries.
- Devcon Brushable Ceramic, Devcon EZ-Spray Ceramic, and Devcon Wear Guard 300RTC simultaneously withstand chemical and abrasive attack, a challenge in the mining industry.
- Devcon’s chemical resistant coatings extend the time between re-application, prolong the life of equipment, and minimize expensive shutdowns.
Contact ITW Performance Polymers Technical Services for help choosing the best chemical resistant coating for your unique situation. Our engineers and technicians have deep application knowledge and are dedicated to providing solutions to your challenges.
View all our Technical Data Sheets and Safety Data Sheets. Need some help? Ask a technical question and find a solution!
Further reading: Durability With Devcon® Protective Coatings: Proven In Multiple Industries and The Top Four Types Of Wear Impacting Industrial Equipment.
For more stories like this, follow ITW Performance Polymers on LinkedIn and sign up for enewsletter in our website footer.