At a coal power plant, coal is sent through a pulverizer which grinds the material into a coarse powder. The coal powder is then sent via screw conveyor to a large industrial furnace equipped with boiler tubes filled with water. The coal powder is burned, heating the boiler tubes and converting the water into steam. This process produces the same steam, which is converted to heat and light energy – the output of the coal plant.
Problem
The screw conveyor, transporting coal to the furnace, faced abrasion wear due to dry coal collecting on the screw conveyor trough and on the screw flights. The constant abrasion wear caused cavitation in the trough, preventing the proper conveying of the coal, vital to plant operations. The screw conveyor trough needed to be rebuilt back to the equipment specification. The client was looking for a long-term solution which would provide long-term wear resistance, limit equipment downtime, and increase productivity.
Solution
Devcon Ceramic Repair Compound was used to restore corroded trough areas while Devcon Brushable Ceramic Red and Devcon Brushable Ceramic Blue coatings provided the required long-term wear resistance.
- For optimal application, the trough was blasted to a white metal status and wiped with solvent.
- Devcon Ceramic Repair Compound was applied to the worn gouges and holes in the trough, repairing areas of cavitation.
- After a 4-hour cure, two coats of Devcon Brushable Ceramic Coating in red and blue were applied with a thickness of 15 mm for a total coating of 30 mm.
- In order to achieve ideal protection from wear and abrasion, the conveyor screw was also coated with Devcon Ceramic Repair Compound, and Devcon Brushable Ceramic Red / Blue coatings at a total thickness of 30 mm.
The versatility of Devcon industrial strength epoxies allowed for differing components of the screw conveyor trough to be repaired with only a few easy-to-use products.
Project Outcome
Simple Installation
A common practice for industrial plants is to weld metal plates on equipment to act as the sacrificial wear protection. However, this can take an extensive amount of time that also requires trained welders to install and carry out the repairs. With Devcon Ceramic Repair Compound and Devcon Brushable Ceramic Red / Blue coatings, plant employees can easily perform maintenance repairs to equipment in under 24 hours.
Long-Term Durability
With 12,000 tons of coal processed each day, this plant needed a solution easier and less expensive than metal plates to withstand heavy and abrasive material. Devcon coatings provided the long-lasting protection from corrosion, abrasion, and impact resistance. The client was also able to identify areas of wear for future maintenance activities by coating the trough and screw with layers of Devcon Brushable Ceramic Red and Devcon Brushable Ceramic Blue.
Limiting Equipment Downtime
Generating consistent power supply for millions of residences and commercial facilities is a necessity. Being able to provide this means keeping plant equipment continually and efficiently running to maintain operations. With Devcon Ceramic Repair Compound and Devcon Brushable Ceramic coatings, the customer was able to quickly and efficiently repair the damage to the screw conveyor trough equipment. Devcon coatings efficiently limited equipment downtime and increased operational efficiency.
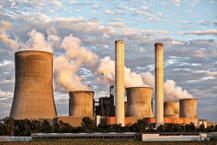
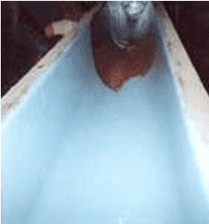
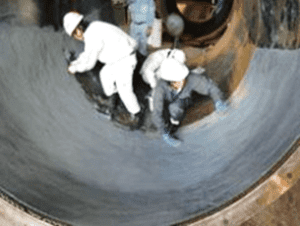
Devcon Wear Guard Fine Load coating has excellent high temperature resistance in both dry and wet environments making it suitable for protecting and extending the life of processing equipment in a variety of industries.