Problem
A petrochemical facility based in the Gulf region had a corroded pressure vessel that needed to be urgently repaired. With signs of cavitation evident within the equipment and increasing risk of leaks, the customer was seeking a safe, quick and economical repair solution.
Replacing the equipment in its entirety was not fast or cost-effective. Welding was not appropriate due to safety concerns and environmental factors. In addition, temperatures in the region could reach as high as 122°F / 50°C. Given most of the repair work needed to be manually applied inside the 108” (9 feet) carbon steel vessel to protect the equipment from corrosion and leaks, the repair work needed to be fast and easy.
Solution
High-performance Devcon Titanium Putty and Devcon Brushable Ceramic coatings were selected to repair and rapidly return the pressure vessel back to service.
- For preparing the surface of the vessel’s internal shell, the bottom half of the vessel was blasted to SA3 – SSPC5 with a surface profile of 80μ to 90μ. The surface profile check test was carried out by the customer to ensure the required specifications were met.
- Devcon Titanium Putty part A and part B were thoroughly blended on the mixing board using a 3” mixing spatula. This was used for filling and fairing the anomalies / defects in the vessel.
- Devcon Titanium Putty was then spread to fill up all the anomalies, then the application thickness was unified over all pitting locations. After curing, the first coat of Devcon Brushable Ceramic was applied using a hand brush.
- The Wet Film Thickness of Devcon Brushable Ceramic was confirmed to be within the acceptable range (350 to 500 microns). An additional coat was applied using the same methodology. No spark was shown by the Holiday detector upon completion.
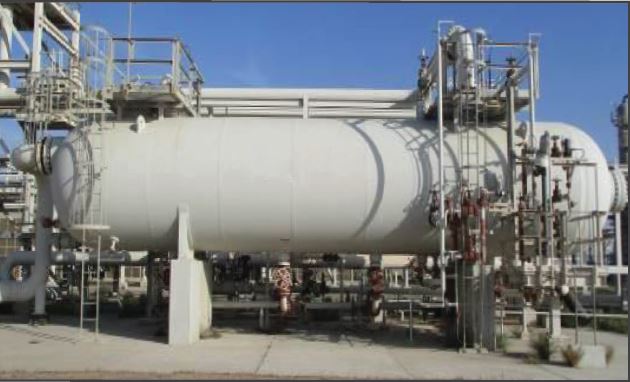
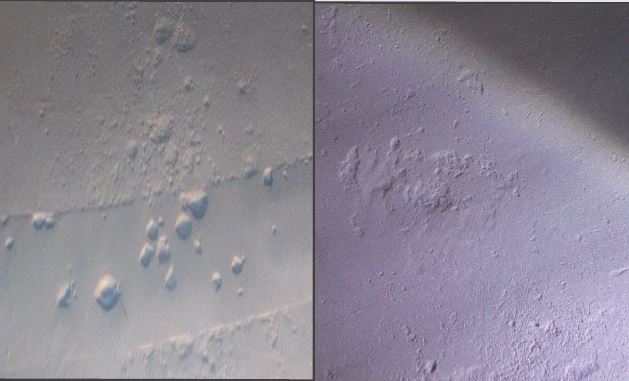
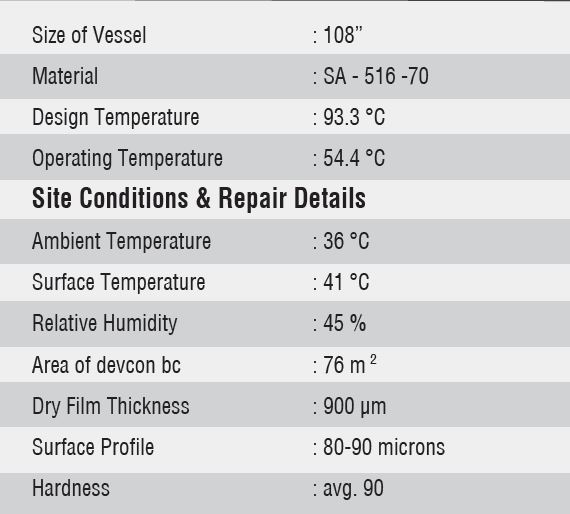
Project Outcome
Highly Durable Coatings
Devcon Titanium Putty and Devcon Brushable Ceramic Blue coatings provide long-term, corrosion protection that restored the pressure vessel to its original and intended operating condition.
Safe Installation
The cold welding that the Devcon repair system offers makes the coatings a far safer alternative to welding at a petrochemical facility; the main idea behind the creation of Devcon in 1947 – avoid hot work (welding) when facing explosive environments.
Quick & Easy Application
Pitting, corroded, and eroded areas were filled and repaired in just a few hours as Devcon coatings are quick to mix and easy to apply.
In addition to the benefit of having a safe, easy application, Devcon Coatings helped extend the service life of the pressure vessel, preventing the need to replace equipment thereby reducing overall maintenance cost and downtime.
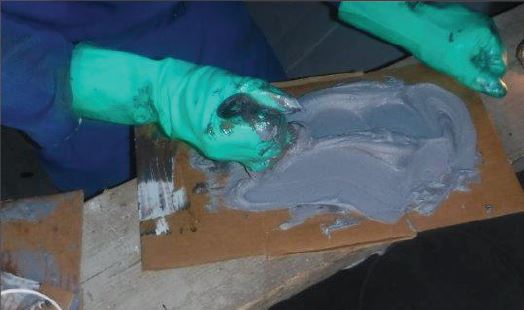
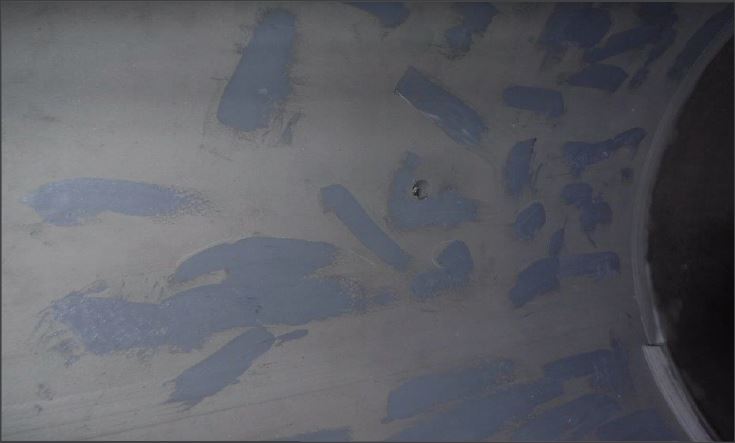
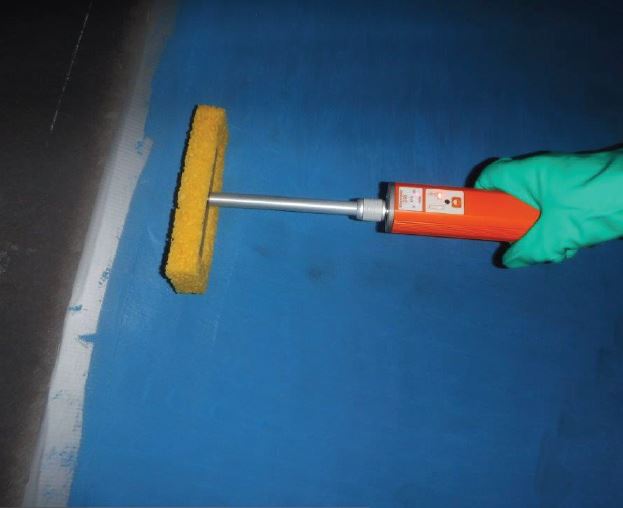
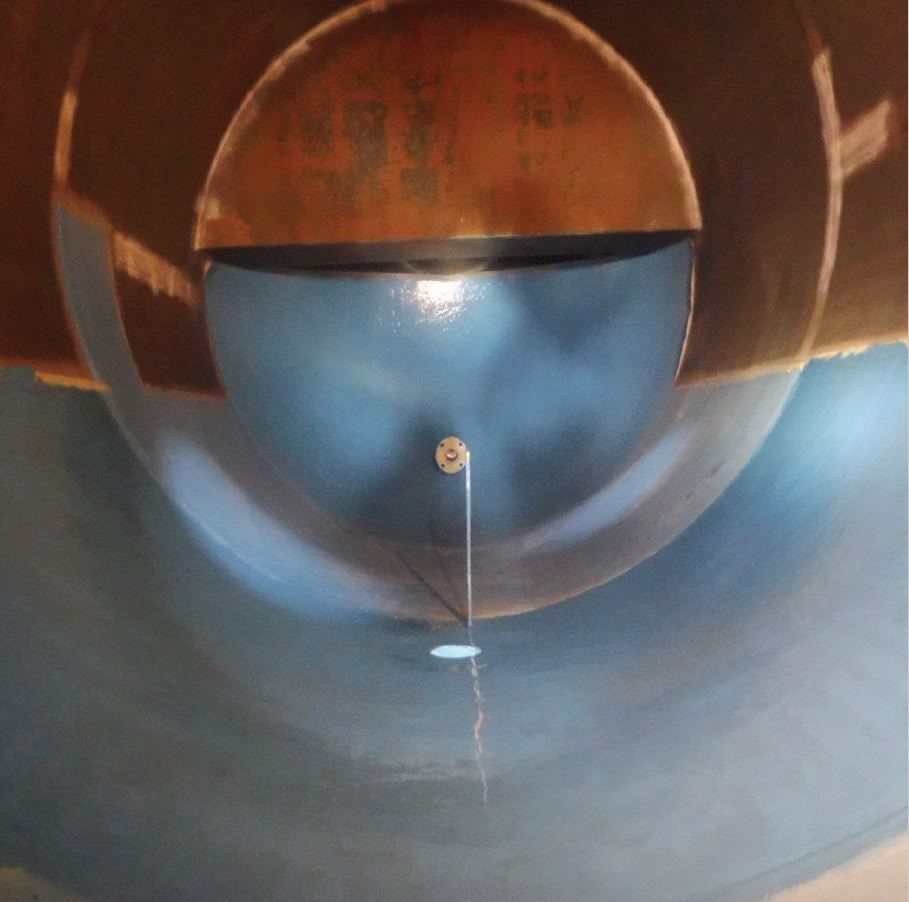