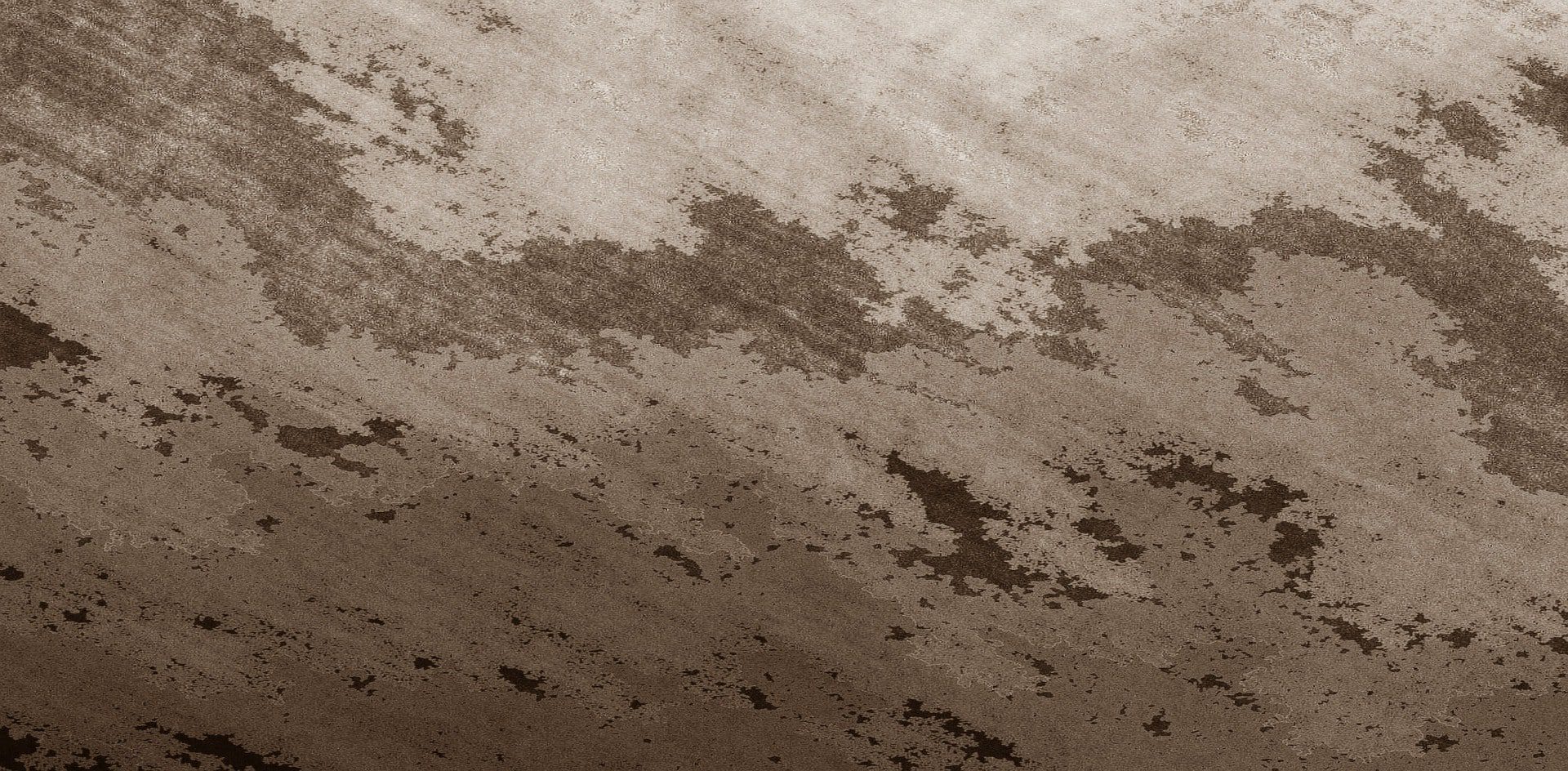
Wear is the damaging, gradual removal or deformation of material of solid surfaces. Causes of wear can be mechanical or chemical. With this definition in mind, there are many reasons to coat industrial equipment like storage tanks, process piping, aggregate chutes and pumps that are made of metal (and at times concrete or fiberglass.) A protective coating, or a sacrificial layer, is applied to increase the service lifespan against the greatest problems of mechanical (Impact, Erosive, Abrasive) and chemical (Corrosive) Wear. Water alone can create both types of wear creating the need to service pumps several times a year. Such protective coatings help keep operations running longer and more efficiently between scheduled preventive maintenance needs.
To gain such extended lifespan from a piece of equipment, it’s necessary to protect the equipment with the correct material resistant to the operating conditions. Keeping in mind that operating conditions are influenced by both environmental and processes conditions, there are coatings on the market today that can be used to protect the equipment such as the coatings manufactured by ITW Performance Polymers which includes the Devcon® brand.
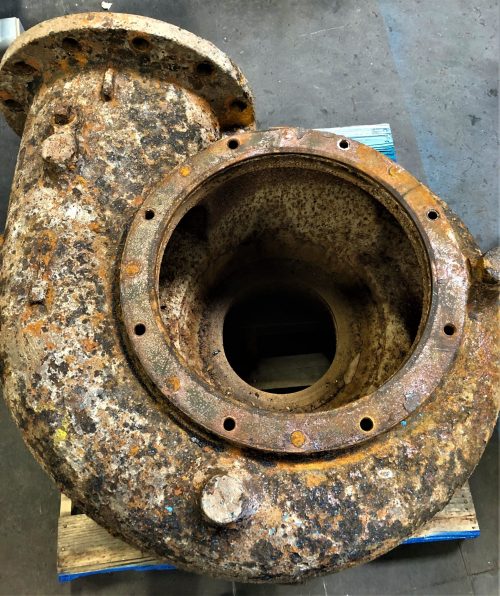
Wear Resistance
As implied, there are many types of wear and scenarios that can influence such wear. For this article, we will focus on what we see as the top four types of wear.
Typical environmental and operating conditions are temperature exposure and more aggressive wear conditions that include but are not limited to Erosive, Abrasive, Impact, or Corrosive Wear. Most times there is a combination of some or all these conditions. An industrial coating can be used to protect against environment corrosion and heating and the operating conditions. The correct coating helps to relieve some of the wear and extend the life of the equipment, but to successfully do this it’s very important to understand what type of Wear Condition you are encountering and what are the types of products that can be used to protect your equipment.
The top four are Impact Wear, Erosive Wear, Abrasive Wear (Mechanical), and Corrosive Wear (Chemical). Each condition requires a different response or approach, from an industrial coating to achieve the correct level of protection. For instance, choosing a corrosive resistant product that is brittle, will fail very quickly if exposed to impact. It is very important to place the correct coating in the correct environment to achieve the desired results. There is not one solution to fit all types of wear. As a result, we recommend end users to work directly with suppliers and manufactures to help chose the proper solution such as those under the Devcon brand. Reach out to a Technical Support specialist for help.
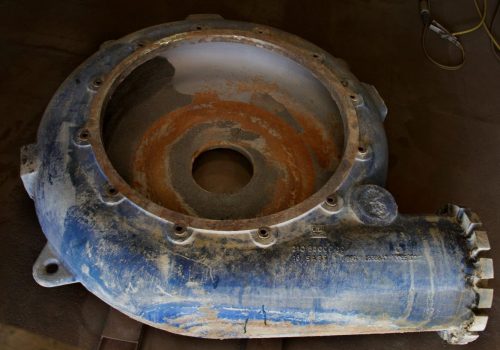
Impact Wear is caused by the falling of a solid product from one level to another and mechanically impacting at a perpendicular angle to a surface, like falling from the end of the belt into a hopper in an aggregate mine. The energy level at impact is determined by the mass of the object and the height from which it falls. This type of wear requires a coating that can help absorb the large range of impact energy directly on the equipment. A suitable sacrificial coating of this type should be brittle so it readily breaks apart and should have the ability to be coated at various thickness suitable to address the various particle size and level of energy generated in the fall.
The best types of products for protection against Impact Wear are specialty epoxy and urethanes. The ideal epoxy systems are designed specifically with specialized fillers that provide energy absorption and flexibility. Similarly, efficient wear protecting Polyurethanes are formulated with complimentary materials to both control flow properties for coating and provide its energy properties. Both technologies are suitable, but each one does tend to offer advantages over the other under various conditions. As an example, when there is a high rate or velocity of Impact Wear then a thick polyurethane coating will often provide a longer lasting protective coating. If there is a high impact energy level in the Impact Wear, then the specialty designed epoxy system, like Devcon’s DFense Blok, may be the ideal thing to protect the equipment from damage.
Erosive Wear is generally cause by a wet slurry. A slurry is a system of solids and fluids that are generally pumped through piping using large slurry pumps. The amount and type of solids in a slurry will define the degree of the erosive wear. Slurry particles can reach sizes of up to 3/8” and have a solid loading of up to 60%. This type of wear focuses highly on the fluid and particle contacting the wall and the velocity at which they are moving. This type of system often also incorporates heat to help maintain a steady viscosity inside the process system. The wear protection products that work best here will maintain a smooth surface and withstand the wear from the high velocity particles moving by.
Note that variances inside the equipment can impart some limitations on the protective product you chose. For instance, on the inside of a pipe, a thin coating is preferred, to maximize the volume of product that can move through the pipe. The best coatings for this environment are generally a thin epoxy or polyurethane coating, such as our Devcon urethanes and Flexane 80 Liquid. For a slurry that is at an elevated temperature or is very corrosive, then an epoxy coating may provide the best protection. However, if Corrosive Wear and temperature resistance are not a concern and the slurry is just aggregate and water, then a polyurethane coating may prove best and the most practical option for the required protection.
Abrasive Wear is generated by the movement of dry material over a surface usually due to shaking, forced air or simply gravity. This particular type of wear is also very aggressive and can quickly cause equipment failures. Abrasive Wear is influenced by a variety of factors including aggregate hardness, shape, mass, and velocity flow. To combat Abrasive wear some of the best performing coatings are beaded epoxy protection systems, such as Devcon Wear Guard High Load. Beaded compounds like this incorporate various ceramic fillers that are encapsulated in a strong epoxy system. These fillers work with the epoxy to provide long lasting protection against Abrasive Wear. Additives such as Coupling Agents and crosslinkers are incorporated into the chemistry to provide toughness and a bond between the epoxy and the ceramic fillers. The better the epoxy system and coupling agent combination, the longer the ceramic beads remain in place, meaning a long protective period between coating maintenance.
Corrosive Wear is caused by chemical and electrochemical reactions between the material being moved and the surface of the processing equipment. This type of wear is caused by the chemical nature of the material makeup, other potential external environmental conditions, or intentionally added processing aids. Protective corrosion resistant Coatings are used on many everyday products to protect them from environmental or material conditions that cause corrosion.
Consider paint on a car or a truck. It’s a coating to protect the vehicles’ parts and body from corrosion, or rust, to ensure a longer life span. Applicators with such chemical corrosive wear do the same to protect their equipment. ITW Performance Polymers manufactures many Devcon branded coatings designed specifically to protect industrial equipment from such type of environmental and operating corrosion. A coating like Devcon Epoxy Coat 7000 AR (Acid Resistant) utilizes specialized and select epoxies to provide its ultimate chemical resistant coating that can be applied as thin as 30 mils. With this unique system it is also much more flexible than standard epoxies widening its protective abilities. Keep in mind, when faced with Corrosive Wear, a thick coating should not be needed. If it is the correct coating is chosen for the job, a thin layer should be sufficient, saving time and cost. The properly chosen corrosion resistant coating should act like the paint on a vehicle and provide the right amount of protection.
Conclusion
The wearing of industrial equipment is a global issue that impacts every market in one manner or another. Coatings, like the those manufactured by ITW Performance Polymers, can be and currently are incorporated as a protective layer in many of these markets all over the globe. Understanding your wear needs and identifying the correct coating for your condition extends the life of processing equipment, reduces the need for emergency shutdowns, and keeps the equipment running smoothly and efficiently. Saving time and money is a real possibility with Devcon coatings.
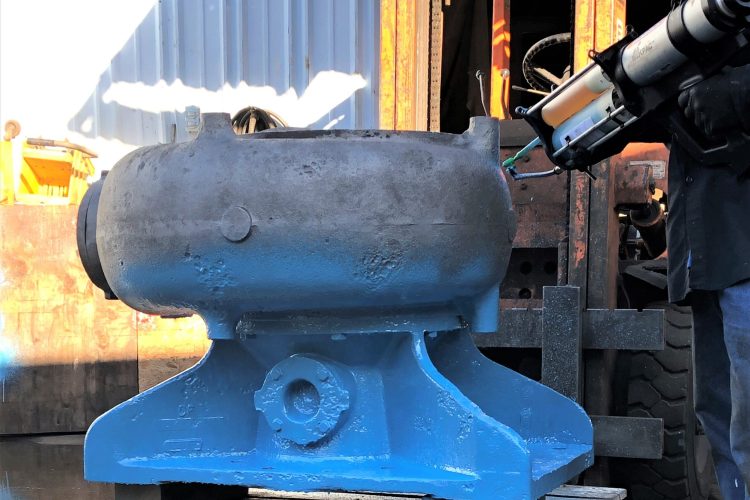
Contact our Technical Services Department for more information on which Devcon coating solution is most suited for your maintenance and repair applications.
View all our Technical Data Sheets and Safety Data Sheets. Need some help? Ask a technical question and find a solution!
Further reading: Durability With Devcon® Protective Coatings: Proven In Multiple Industries and Long-Lasting, Easy-To-Apply Room Temperature Cure Coating That Increases Equipment Life.
For more stories like this, follow ITW Performance Polymers on LinkedIn and sign up for enewsletter in our website footer.