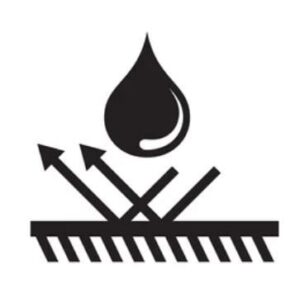
Introduction
The global cost of corrosion is estimated to be US$2.2 trillion, which is equivalent to 3% of the global GDP (source: The World Corrosion Organization). By using available corrosion control practices, it’s estimated that savings between 15%-35% of the cost of corrosion could be realized. These costs typically do not include individual safety or environmental consequences. Through near misses, incidents, forced shutdowns (outages), accidents, etc., several industries have come to realize that the lack of corrosion management can become very costly. With a strong corrosion management plan, significant cost savings can be achieved over the lifetime of an asset. Industrial coatings are an effective tool to fight corrosion.
Corrosion Basics
Corrosion (deriving from Latin ‘corrodere,’ which translates to ‘gnaw to pieces’) involves the deterioration of a substance, usually a metal.
Steel is the most common material used in construction next to bituminous material. Corrosion could be considered as the reverse process of steel manufacturing. Steel is made in the steel mill where an ore (commonly iron oxide) is subjected to a large amount of energy to extract the iron from it. All the energy introduced to refine steel from its ore, makes the resulting product naturally unstable. Because nature seeks to reach the lowest energy state as it is the most stable, under the right conditions, iron is prone to convert back to the more stable iron oxide or corrode.
The environment and manufacturing conditions produce the fundamentals that create corrosion. In order for corrosion to occur, certain conditions and elements are essential. These are collectively referred to as the corrosion cell and include:
- Anode
- Cathode
- Metallic pathway (or external conductor)
- Electrolyte
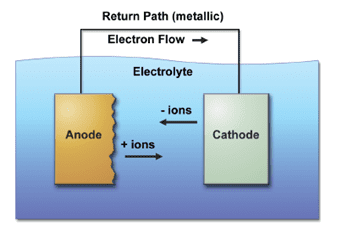
The mechanism for corrosion protection varies, depending on the particular material used. Protective industrial coatings represent the most common and extensively used corrosion protection system for metal structures. The properly chosen protection system can isolate the substrate from the environment (i.e., the electrolyte), and is generally known as barrier protection. However, it important to have a definition of protective coatings or mechanisms to ensure the right solution is achieved. For example, fusion bonded epoxy is a great coating, but is it the right coating for a concrete pipeline?
Corrosion Protection Coatings as a Solution
Most markets, including industrial, architectural structures and non-industrial commercial enterprises rely heavily on industrial coatings for the protection of manufacturing equipment and other important assets. In a general sense, coatings are corrosion inhibitors. They are defined as a thin layer of solid material on a surface that provides improved protective, decorative, or functional properties. More specifically, they are typically made of powder, liquid or a putty composition that, after application to a surface, is converted into a solid protective, decorative, or functional adherent film.
Applying the protective coating to the surface of the metal or asset is the mechanism to protect the substrate from corrosion. The coating itself becomes the barrier that physically isolates a substrate from the environment causing corrosion. Understanding the standard coatings definition and what the expectation is for the coatings meaning will make focusing on the product for your application easier.
The coating barrier protects against corrosion through one of the following ways: They block necessary elements from coming to together to start the corrosion process, actively prevent the electrochemical reaction from occurring, or they cause the corrosion process in a direction or form, that is will not harm the asset.
Finally, keep in mind that not all coatings protect the same. Properly designed or chosen protective coatings are effective against chemical attack, general and localized corrosion – pitting, crevice, and galvanic corrosion. Similarly, some coatings or the improper choice, can afford protection, but they may be limited if not properly matched with the materials and environment. One common question is, “What is powder coating if not a protection against corroded metal?” Powder coated steel is highly resistant to rust, but up to a certain point. Looking at the environment the metal is in has a large affect.
Devcon Coatings for Erosion & Corrosion Resistance
For more than 60 years, Devcon® epoxy coating solutions have provided an efficient way to protect high value equipment against corrosion. Devcon ready-to-use coating liquids and putties provide proven durable protection against chemicals, corrosion and erosion under harsh environmental and industrial conditions.
A few of our most common solutions for the industry:
Devcon Brushable Ceramic: Used on pumps, heat exchangers, vessels, water boxes, and impellers.
Devcon Ceramic Repair Putty: Rebuild worn pump casings and suction plates; repair tube sheets, heat exchangers, and other circulating water.
Devcon EZ-Spray Ceramic: Seal and protect new equipment exposed to erosion and corrosion; protect pump casings, impeller blades, gate valves, water boxes, flotation cells, fan blades and scrubbers; rebuild heat exchangers.
Devcon Epoxy Coat™ 7000AR: Used on chemical storage tanks, dike walls, and containment areas where chemical resistance to acids is needed.
Devcon Wear Guard™ 300RTC: High temp protection for flotation tanks, scrubbers, ash handling systems, pipe elbows, screens, and chutes; recontour chippers, bins, hoppers, bunkers, separators, diester tables; protect exhausters, chutes, launderers, housing fans and breakers.
Devcon Wear Guard Fine Load: Used on slurry pumps, scrubbers, screens, and screw conveyors.
Devcon DFense Blok®: Impact and wear resistant coating for scrubbers, ash handling systems, pipe elbows, screens, chutes, chippers, bins, hoppers, bunkers, separators, digester tables.
Conclusion
Corrosion and wear are natural processes that can be controlled with the use of the proper protective coatings. The Devcon range of industrial coatings has a long history of successfully protecting a variety of equipment. Whether your team is trying to prevent galvanic corrosion, looking for cathodic protection or frustrated with the rusting of steel, our team can assist you in finding the right industrial coatings to protect your equipment. If you want to receive more information, please reach out to our Technical services team. We offer corrosion inhibitors and erosion & corrosion resistance through easy-to-use solutions.
Contact ITW Performance Polymers Technical Services for help choosing the best chemical resistant coating for your unique situation. Our engineers and technicians have deep application knowledge and are dedicated to providing solutions to your challenges.
View all our Technical Data Sheets and Safety Data Sheets. Need some help? Ask a technical question and find a solution!
Further reading: Durability With Devcon® Protective Coatings: Proven In Multiple Industries and The Top Four Types Of Wear Impacting Industrial Equipment.
For more stories like this, follow ITW Performance Polymers on LinkedIn and sign up for enewsletter in our website footer.