To reduce your assembly costs, increase productivity and improve the quality of your finished components – look for an answer in your structural adhesive.
Plexus® acrylic adhesive solutions have helped manufacturers in the bus, truck and rail manufacturing to maintain and exceed existing transportation industry standards.
Suitable for bonding the vast majority of thermoplastics, metal to metal bonding, and composite materials, Plexus ensures durable bonds, offering unlimited possibilities for design engineers and production managers. By chemically fusing plastics and composites, Plexus creates bonds so strong the adhesive will outperform the substrate. In metal bonding, Plexus adds value in applications where aesthetic appearance is important and bond strength is crucial.
Plexus structural adhesives can help reduce assembly costs in the transportation industry by:
- Minimizing or eliminating the need for surface preparation
- Curing at room temperature
- Simplifying assembly processes and shortening assembly time
- Guaranteeing excellent fatigue and impact resistance
In addition to improved design freedom and reliability, working with Plexus gives you access to our fully comprehensive technical support and the outstanding customer service expected from a leading global company.
We believe the importance we place on building strong and lasting relationships with our customers is a large part of our continuing success. We work in close collaboration with our customers, striving to understand all aspects of their bonding requirements and meet their exacting specifications.
QUALITY YOU CAN RELY ON
Our unrivaled commitment to quality is delivered in every adhesive we manufacture, providing our customers with confidence in the reliability of our products.
- Test programs and comprehensive support to aid design and production using customers’ own substrates
- Customer programs to establish environmental and in-service performance
- Expert technical and sales support, with guidance in product selection, joint design, application methods and equipment support
- Access to our global distribution network via strategic partners
To receive a detailed overview of how Plexus can help, please contact us.
Structural Adhesive Products
Methacrylate structural adhesives are commonplace in highspeed production processes and offer engineers a range of benefits from joint design to manufacturing efficiency.
To select the most suitable structural adhesive, we recommend our customers consider the following factors:
- Design parameters
- Substrates used
- Production environment
- Bond strength requirements
Plexus recommends the following adhesive ranges for use in transportation applications:
300 SERIES
Includes both 1:1 and 10:1 general purpose adhesives
Main benefits:
- Broad adhesion
- Excellent impact resistance
- Little or no surface preparation
- Good environmental durability
- Aesthetic finish to the component
- High shear strengths up to 24MPa
Ideal for bonding:
400 SERIES
A multipurpose range of 10:1 adhesives
Main benefits:
- Excellent elongation
- High chemical and impact resistance
- Wide range of open and working times to suit specific applications
- Little or no surface preparation
- High shear strength
- Tough and durable bonds
Ideal for bonding:
Composites and plastic components
800 SERIES
Metal Bonding series of fast curing, structural adhesives
Main benefits:
- Strong yet flexible
- Excellent adhesion
- Eliminates need for primers
- Eliminates all or most surface preparation
- Allows users to move away from traditional methods such as mechanical fastenings, riveting, welding
Ideal for bonding:
Variety of ferrous and non-ferrous metals including aluminum, stainless steel and carbon steel
Superior strength, all-purpose structural adhesives manufactured to bond even the toughest substrates
Main benefits:
- Primerless adhesion
- Easy to use 1:1 ratio
- Excellent environmental resistance
- Extremely durable
- Lower odor
Ideal for bonding:
Composites, nylons, aluminum, galvanized, steel, coated metals, most thermoplastics.
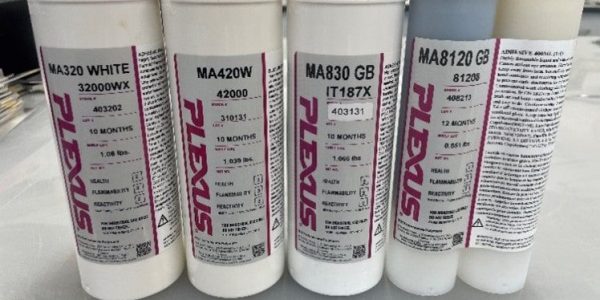
The Plexus equipment range also includes manual and pneumatic dispense dispensers to suit both 1:1 and 10:1 cartridges, specifically for dispensing our adhesives, and a range of static mixers to suit most applications.
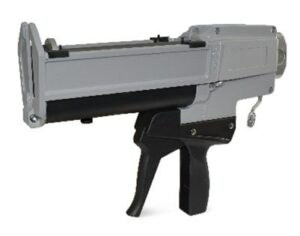
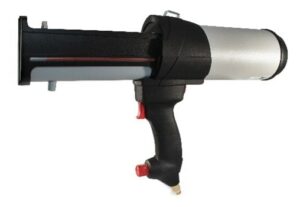
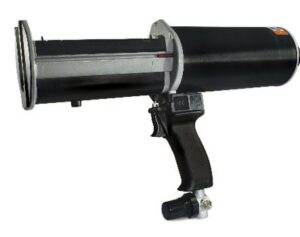
Structural Adhesive Testing
Although structural adhesives have revolutionized manufacturing and assembly industries, the technology is less well understood in comparison to traditional methods of joining substrates.
Our challenge is to demonstrate that structural adhesives outperform traditional methods in terms of improved aesthetics, durability, and fatigue resistance.
At Plexus we have a specific test program to test the type and level of stress a joint will experience over its service life.
Tests simulate vibrations, harmonics and repeated cyclic loading together with the chemical and environmental exposures in transportation assemblies to assist our customers with data to relate to their product design and application longevity.
Our static and dynamic testing offers valuable data to the designer of assemblies and ensures long-term part performance.
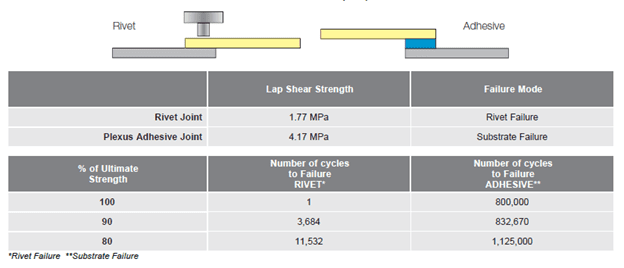
In the example above, using an X diam. aluminum rivet etc., not only does the adhesive joint provide a stronger bond than the rivet, but when tested for fatigue, Plexus adhesives outperform this riveted joint by more than 98%. Results will of course vary depending on the type and material of the rivet as well as the Plexus selection.
Fatigue resistance is important when a bonded joint is likely to be exposed to dynamic applications that will see vibration, shock or impact. Plexus methacrylate adhesives outperform other adhesive technologies and systems.
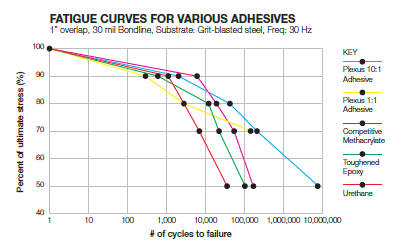
TESTING METHODOLOGY
Samples of each joining method are first tested as static lap shears that are pulled to failure at a constant speed. The average maximum stress is referred to as the ultimate shear strength which represents the load that a joint can bear in a single cycle. Samples are then cyclically fatigue tested to various percentages of their ultimate strength. Cycles are performed at a rate of 30 cycles per second (30 Hz).
North American & European Technical Facilities
Plexus Technical Centers offer our customers facilities that deliver comprehensive and technically proven solutions.
Within our laboratories we have the ability to carry out bulk polymer and mechanical testing including tensile, impact, fatigue, thermal, climatic and environmental testing on a variety of substrates and temperatures. Combining our extensive historical database of material screening and applications knowledge with our in-house experts, we use predictive testing to share data to simulate the environmental effects on the bond performance.
All testing and subsequent adhesive selection is therefore selected to each customer’s individual needs to provide professional advice for your business.

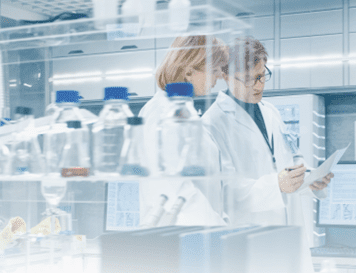
View all our Technical Data Sheets and Safety Data Sheets. Need some help? Ask a technical question and find a solution!
Further reading: Thixotropy, Viscosity and Rheology … Oh my!, What is fixture time anyway?, and Is it strong enough?.
For more stories like this, follow ITW Performance Polymers on LinkedIn and sign up for enewsletter in our website footer.