Conveyor belt splicing is a technique of conjoining two pieces of rubber belt material. Splicing is necessary when elongating a conveyor belt or repairing holes to bind the damaged rubber. Splicing repairs generally fall into two major categories: Vulcanization splicing and mechanical splicing. Vulcanization is the reaction and hardening of a new rubber material, while mechanical splicing is the process of attaching hinged fasteners to the conveyor belt. In comparing techniques, both are effective but damage to splicing is almost always inevitable.
Problem
At a copper mine, mechanical splicing is utilized to conjoin two large sections of a conveyor belt used to transport ore raw material to the processing facility. Metal fasteners used in the mechanical splicing faced consistent wear and corrosion due to handling a large influx of abrasive ore as well as exposure to harsh environmental conditions. As a result of corrosive and abrasive wear, the metal splices began to weaken, potentially creating more or new damage to the conveyor belt. The customer was looking for a long-term, durable coating that would withstand continuous wear and abrasion.
Solution
Devcon R-Flex coating was used to repair and protect the damaged clips.
- Using recommended product instructions for optimal substrate adhesion, the belt was cleaned, and metal clips were primed with solvent.
- An area of 8” on either side of the belt fasteners was abraded to prepare the substrate for Devcon R-Flex application.
- Devcon Metal Clip primer was brushed onto the fasteners and left for ten minutes to dry.
- Devcon R-Flex was then easily mixed and poured over the damaged metal clips at a thickness of ⅛”.
- The repair area was then left to cure for a total of 90 minutes before returning the conveyor belt back to service.
Project Outcome
Increase Equipment Life
This copper mine was looking for a solution which would protect the mechanical clips and further extend the life cycle of their conveyor belt. Inspection at the next planned shutdown revealed that the repaired clip section coated with Devcon R-Flex exhibited none of the wear and corrosion problems as the same sections made without it. By extending the life cycle of the conveyor splicing clips, Devcon R-Flex helped reduce maintenance costs.
Reduce Maintenance Time
Replacing metal fasteners is a complex repair that can take hours and drive-up total time spent on maintenance repairs. With Devcon R-Flex coating, maintenance time was limited to only 90 minutes, resulting in minimal equipment downtime.
Easy-to-Use Application
Devcon R-Flex was applied to the metal fasteners in only a few simple steps. With this easy-to-use application, Devcon R-Flex can be applied by plant maintenance personnel with minimal training, compared to vulcanization splicing which requires substantially more specialized experience, time to process and cure.
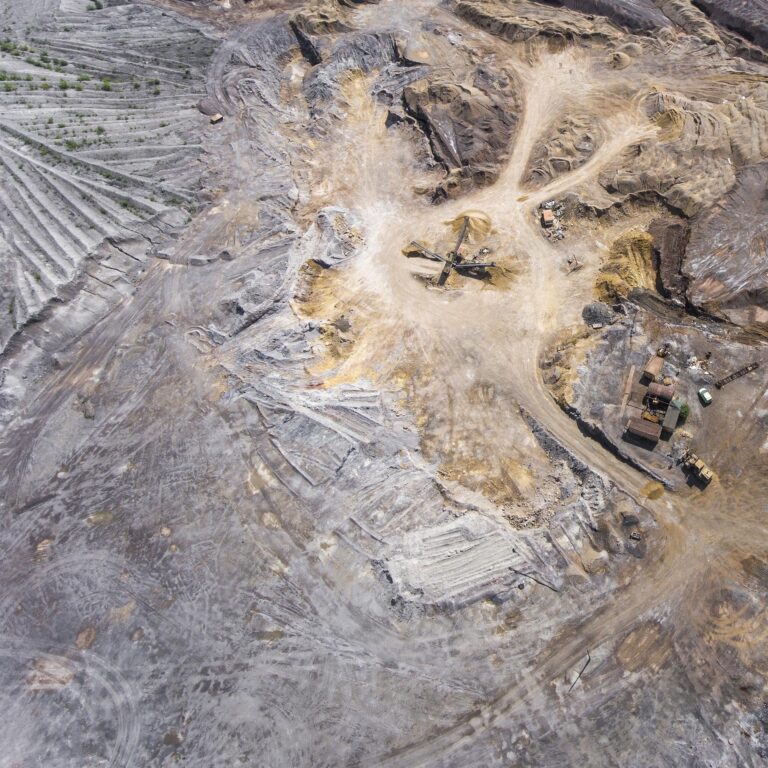
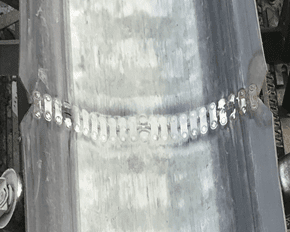
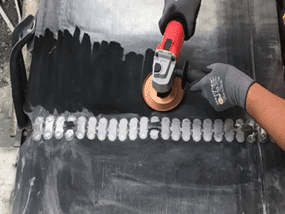
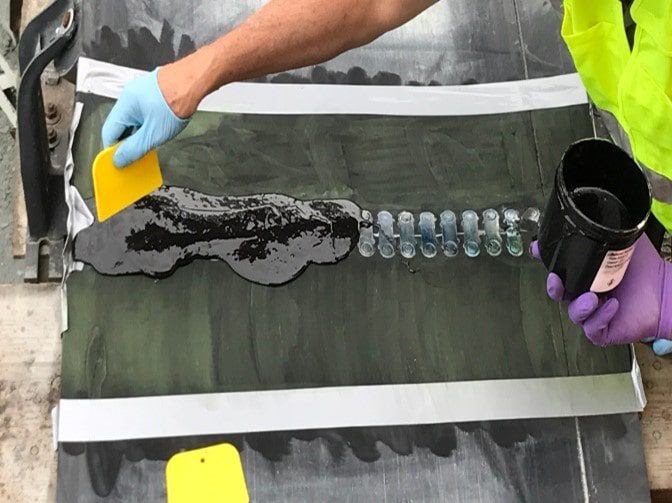