Problem
As part of the dry coke quenching system, the pressure cyclone at a steel plant uses high temperature air to dry coke for optimal burning. Despite allowing for a more environmentally friendly alternative to wet coke quenching, this system did not come without its challenges. The process cyclone, made of ceramic tile, began to wear and fail at the seams sooner than expected, due to high temperature exposure and high impact handling of raw material. The equipment had to be taken offline and the client contemplated full replacement of the ceramic tiles as well as industrial strength epoxy coating solutions.
Solution
After evaluating all repair solutions, Devcon Wear Guard High Temp was chosen due to its high temperature resistance and durability.
- The cyclone was emptied of remaining coke and cooled to safely apply the industrial strength epoxy.
- The tiles were then abraded to ensure optimal adhesion to the epoxy coating and cleaned in high areas of wear, predominantly at the seams of the tiles.
- Devcon Wear Guard High Temp ceramic bead reinforced epoxy system was easily applied to the seams of the cyclone in a few application steps.
- In order to speed up the final cure of the coating, the cyclone was turned on to a higher temperature.
Project Outcome
High Temperature Resistance
This steel plant was looking for a product that would protect the cyclone against extreme temperatures necessary for coke drying. Devcon Wear Guard High Temp was able to deliver on all fronts. With temperature resistance up to 450ºF / 232ºC, ceramic tiles and seams were equipped with better heat protection to prevent wearing and further damage.
Lowering Repair Costs
The client contemplated fully replacing the ceramic tiles which could cause an extended downtime and an increase in maintenance costs for the plant. With Devcon Wear Guard High Temp, the repair solution cost a fraction of the cost necessary to fully replace the ceramic tile. A quick repair time also reduced equipment downtime.
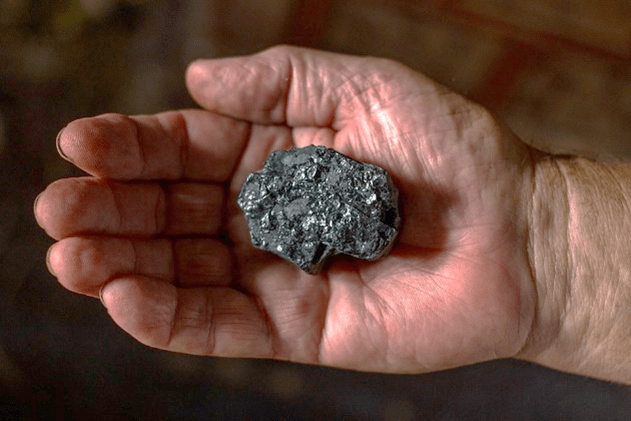
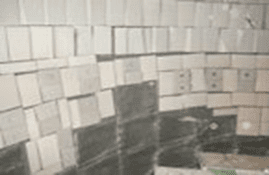
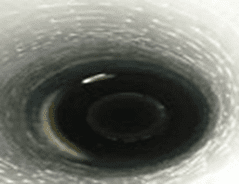
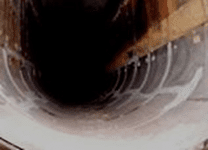